Aluminum Anodizing Services
We understand that a CNC part’s longevity, appearance, and overall quality are often determined by its surface finish. That’s why we’ve meticulously honed our surface finishing services, emphasizing premium aluminum anodizing services.
What is Anodizing?
Anodizing is one of the most revered processes in the metal finishing industry, heralded for its unique combination of aesthetics, durability, and corrosion resistance.
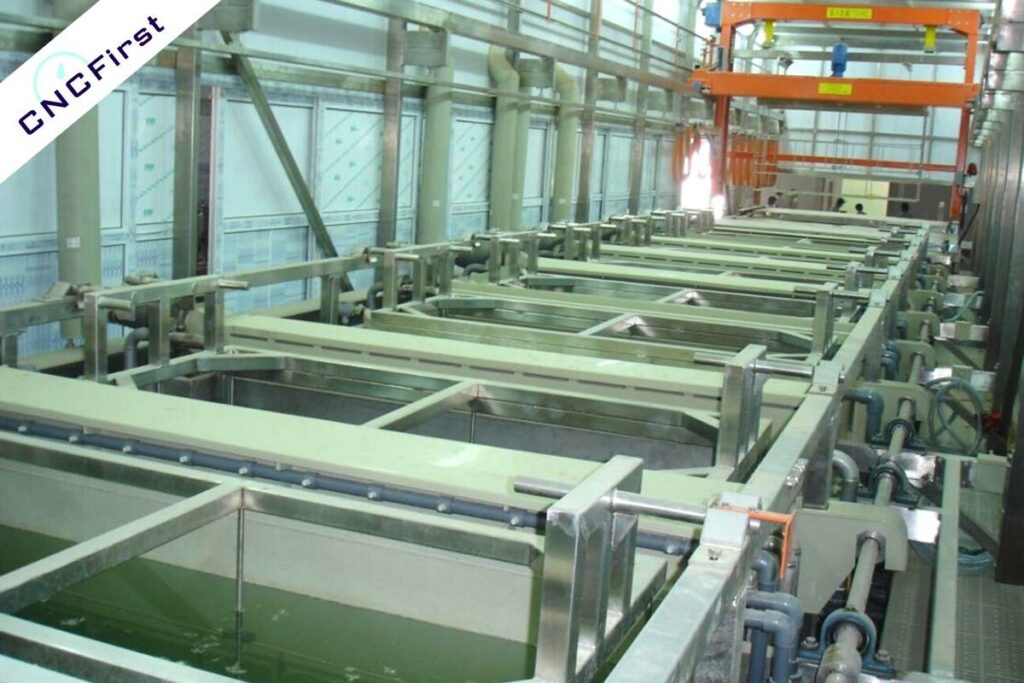
Anodizing is an electrolytic passivation process that converts a metal surface into a decorative, durable, and corrosion-resistant anodic oxide finish. Most commonly applied to aluminum, the process enhances the natural oxide layer of the metal, resulting in a surface that’s tougher than the raw material itself.
The oxide layer is a combination of buildup on the surface of the aluminum part and penetration into the metal. This aluminum oxide layer is not applied to the surface like paint or plating; it originates from the metal substrate and is composed entirely of aluminum oxide, so it cannot chip or peel.
Types of Aluminum Anodizing Services We Offer
We offer a diverse range of anodizing solutions to cater to your CNC component needs. Here’s a closer look at the types of aluminum anodizing services we proudly offer:
Type I Anodizing (Chromic Acid Anodizing)
- A pioneer in the anodizing domain, Type I employs chromic acid to produce a thin but highly protective oxide layer.
- Ideal for delicate parts and those requiring minimal dimensional changes, this method offers a lightweight, even coating.
- It's especially beneficial for aerospace components and other applications where top-tier corrosion resistance is paramount without significantly increasing surface thickness.
Type II Anodizing (Sulfuric Acid Anodizing)
- Balancing aesthetics with durability, Type II is the most widespread form of anodizing.
- Utilizing sulfuric acid, it crafts a versatile oxide layer that's thicker than Type I, granting enhanced protection while allowing for a broader spectrum of color finishes.
- From consumer electronics to automotive parts, this method caters to many industries, making it a go-to choice for many.
Type III Anodizing (Hard Anodizing)
- Type III, also known as hard anodizing, steps in when standard protection doesn't suffice.
- Engineered for extreme conditions, this method produces a substantially thicker oxide layer, exponentially increasing wear resistance.
- Particularly suited for parts subjected to high friction or those operating in aggressive environments, hard anodizing guarantees longevity and unparalleled resilience.
Anodized Aluminum Parts
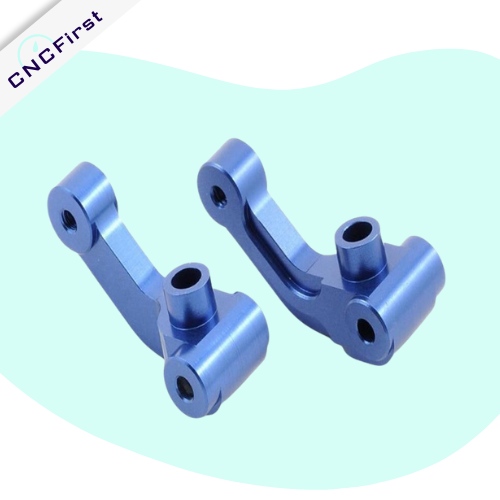
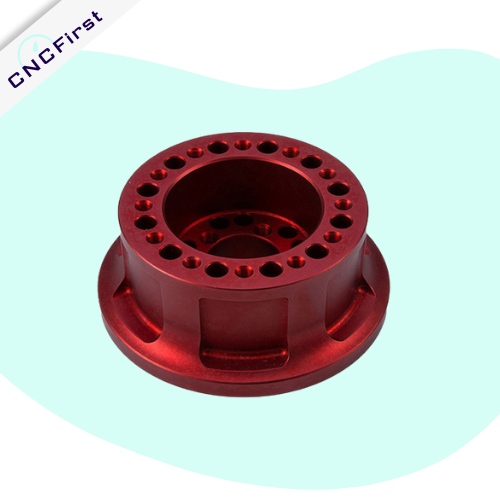
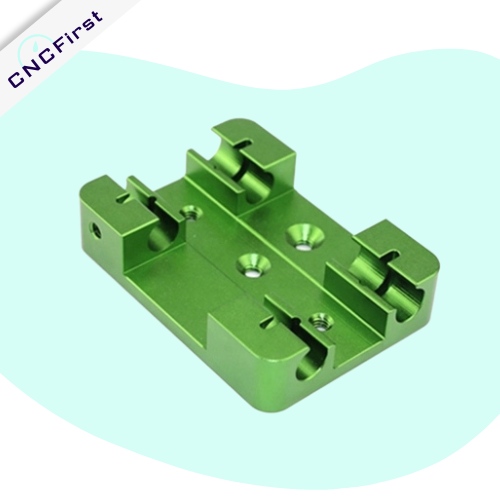
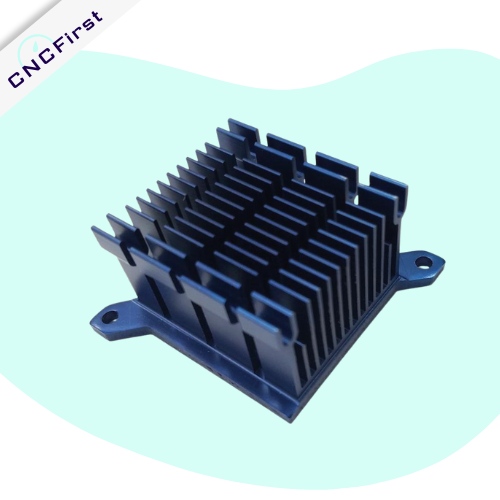
Design Considerations for Aluminum Anodizing
- Alloy Selection: Different aluminum alloys react differently to the anodizing process. Choose an alloy known for achieving a uniform and aesthetically pleasing finish.
- Component Geometry: Avoid deep recesses or sharp internal corners, which might result in uneven anodizing or color pooling.
- Surface Preparation: Pre-treatment processes like polishing or bead blasting will affect the final appearance. Decide on the desired surface finish before anodizing.
- Thickness Requirements: Determine the desired thickness of the anodic layer. Hard anodizing, for instance, will result in a thicker oxide layer than conventional anodizing.
- Racking Points: Identify non-critical areas for racking. These points will be left un anodized during the process and must be strategically placed.
- Sealing Process: Choose the appropriate sealing process post-anodizing to enhance corrosion resistance and dye retention.
- Dimensional Tolerances: Remember that anodizing can slightly alter the part's dimensions—design with this in mind, especially for tight-tolerance components.
- Longevity and Wear: If the component is exposed to high-wear conditions, consider hard anodizing or specify a thicker anodic layer.
Benefits of Our Aluminum Anodizing Services
Enhanced Durability
The machinery world is unkind to components, often subjecting them to wear, tear, and environmental stresses. Our anodizing technique fortifies CNC parts, increasing their resistance against such challenges. This not only prolongs the lifespan of your components but also ensures they function optimally throughout their lifecycle.
Color Diversity
Branding and aesthetics go hand in hand. With our vast array of color options, you can tailor the look of your CNC components to align with your brand or design guidelines. From translucent subtleties to bold vibrancy, we ensure your parts resonate with your vision.
Pristine Finish
First impressions matter. Whether it's a consumer product or an industrial component, its finish speaks volumes about its quality. Our anodizing services guarantee a smooth, even, and premium appearance that stands the test of time. The results? CNC parts that look as professional as their performance suggests.
Electrical Insulation
Specific applications require CNC components to have non-conductive properties. Anodizing naturally enhances the electrical insulation capabilities of metals. With our aluminum anodizing services, you can be confident that your CNC parts will adhere to stringent non-conductive requirements, ensuring safety and functionality in all electrical contexts.
Other surface finishes for CNC parts
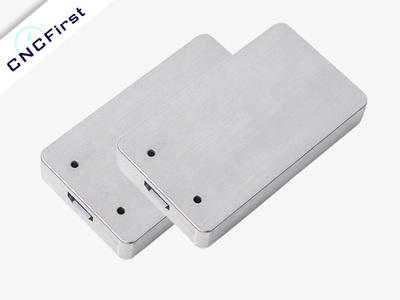
Brushing is a process that ensures the cleanliness and accuracy of a final product. This involves using wire brushes to remove metal burrs, shavings and any other contaminants from the surface of the part.
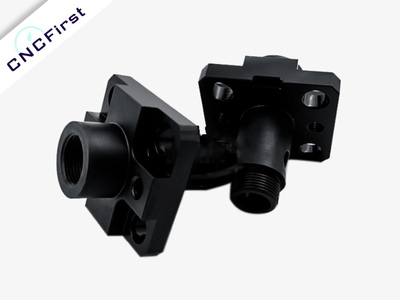
Black oxide is also referred to as blackening, and it adds a matte black finish to the metal, making the surface look darker in contrast to its original state. It makes the CNC parts appear more aesthetically pleasing while also protecting it from corrosion and rusting.
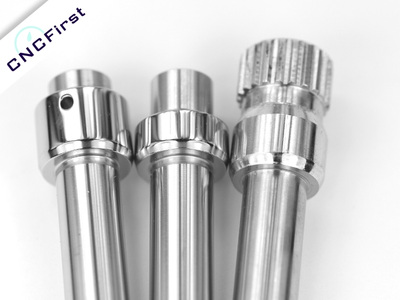
The goal of polishing is to enhance the natural beauty of the material so that it looks better than when it was first created.
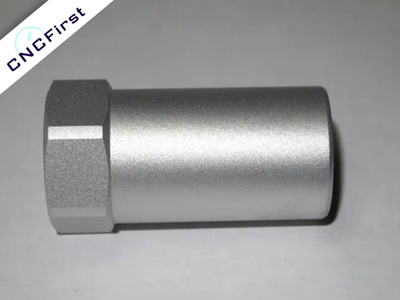
Bead blasting is a finishing process that uses small, round particles to force abrasive material onto any given surface. This process can improve the surface of CNC parts by smoothing and rounding out rough edges, removing burrs and other surface imperfections.
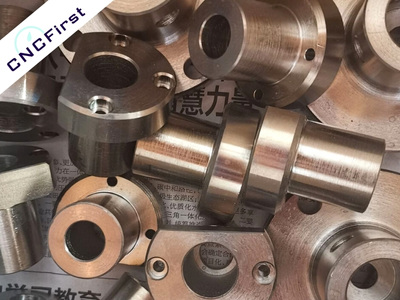
Electroless nickel plating
Electroless nickel plating is an incredibly useful process for adding a protective layer of metal to a variety of surfaces. It involves immersing the object in an electroless nickel solution, which then deposits nickel onto the surface.
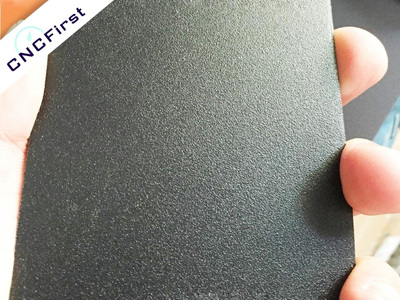
Powder coating uses a fine powder that is electrostatically charged and then sprayed onto the desired product. It finally forms an incredibly durable finish that can withstand harsh weather conditions, corrosion, chemicals and abrasion far better than traditional wet paint.
Anodizing FAQs
Why does the color range differ between aluminum alloys when anodized?
Different alloys have unique compositions, affecting color consistency and brightness during the anodizing process.
How long does the aluminum anodizing process take?
The duration of the anodizing process largely depends on the desired thickness of the anodic oxide layer and the project’s specific requirements. Generally, standard anodizing can take 30 minutes to a couple of hours.
However, hard anodizing, which results in a thicker layer, may require more time. It’s essential to note that preparation and post-treatment procedures can add to the overall duration. To get a precise timeframe, it’s always best to discuss the specifics of your project with an anodizing professional.
Can previously anodized parts be re-anodized?
Yes, previously anodized parts can be re-anodized. However, the original anodic layer must be stripped off before re-anodizing, ensuring the metal reverts to its bare state. This is typically done using chemical solutions or immersing the part in a de-smutting tank.
Once the old layer is completely removed, the part can undergo the anodizing process again. Each stripping procedure can lead to minimal material loss, which might affect the component’s final dimensions.
What colors are available for aluminum anodizing?
Anodizing aluminum offers a diverse palette of colors, largely due to the ability to dye the porous oxide layer formed during the process. Common colors include clear, black, gold, blue, red, and green.
However, many other hues and shades can be achieved with specialized dyes. Clear anodizing, or natural anodizing, retains the metal’s inherent metallic appearance while offering protection.
Collaborating with an anodizing expert is recommended for specific color requirements or custom shades to ensure desired results.
How does anodizing affect the dimensions of CNC parts?
Anodizing impacts the dimensions of CNC parts but in a controlled and predictable manner.
When a part is anodized, a portion of the added oxide layer grows inward, consuming some base metal, while the remainder expands outward.
For example, if the anodic layer is 0.001 inches thick, the part’s dimension might increase by approximately 0.0005 inches outwardly while consuming an equal amount inwardly.
This slight dimensional change is crucial to consider, especially for parts with tight tolerances.
Consulting with an anodizing specialist can clarify how the process might specifically impact your CNC component’s dimensions.
Preparing Your aluminum CNC Parts for Anodizing
Don’t leave the final touch to chance. Ensure your components get the top-tier treatment they deserve. Our team is ready to guide and assist in bringing out the best in your CNC parts with our expert anodizing services. Ready to elevate the finish and functionality of your components? Contact us today for anodized aluminum parts.