Bead Blasting Services
Elevate the aesthetics and functionality of your CNC components with our bead blasting services. Harnessing advanced techniques, we ensure impeccable results tailored to your specifications. Trust in our expertise to deliver precision and quality. We provide the finest metal surface finishing solutions in the industry.
Introduction to Bead Blasting Finishing
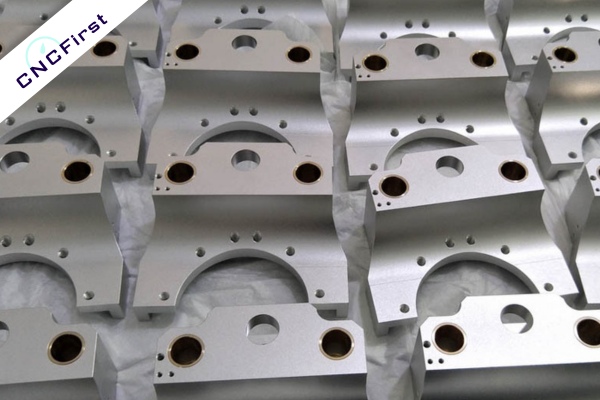
Bead blasting is a specialized surface finishing technique widely employed in CNC machining. It proficiently eradicates surface imperfections by propelling fine bead particles at high velocities onto CNC parts, leaving behind a smooth, satin finish.
Beyond aesthetic improvements, bead blasting plays a pivotal role in enhancing the functional attributes of components. This method prepares surfaces for subsequent treatments like anodizing and ensures longevity and durability.
Applications of Bead Blasted CNC Parts
Industries globally recognize the superiority of bead-blasted parts. These applications include: Critical aerospace components; High-end automotive parts; Precision medical devices; Electronic housings; Tailored projects demanding a unique finish.
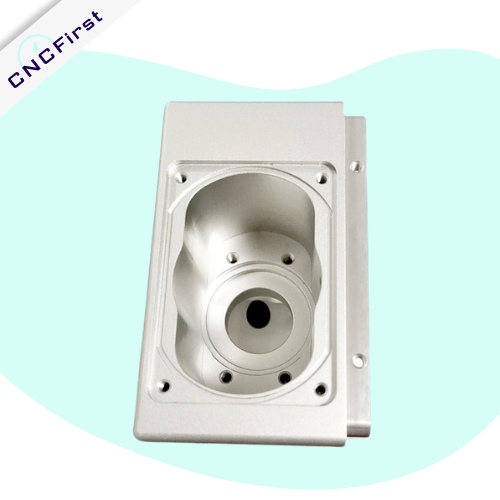
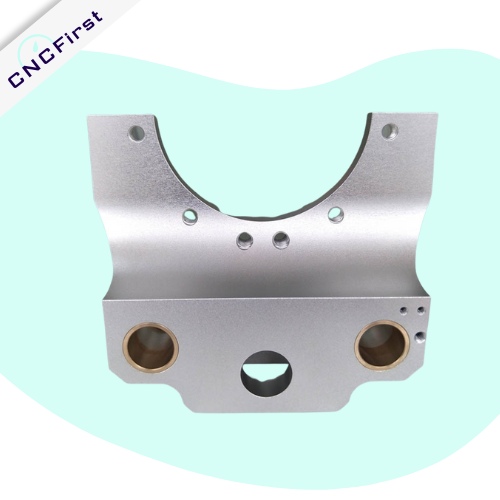
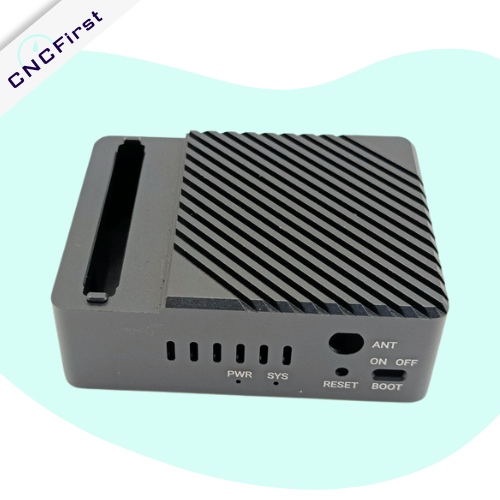
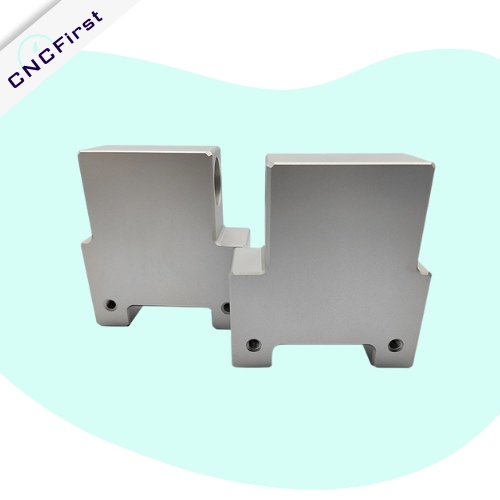
Benefits of Choosing Our Bead Blasting Services
Enhanced Aesthetics:
Our bead blasting services ensure that CNC parts exhibit a uniform, matte finish, free from blemishes and inconsistencies.
Burr and Defect Removal:
One of the most practical benefits is the removal of burrs and other minute surface defects that might impair the component's functionality or assembly compatibility.
Augmented Wear Resistance
Bead blasted surfaces demonstrate a notable resistance to wear and tear, adding to the longevity of CNC components.
Ideal Surface Preparation:
Bead blasting acts as a precursor for other treatments. Creating a clean, textured surface facilitates better painting, coating, or anodizing adhesion, ensuring these treatments last longer and look better.
Design Considerations for Bead Blasting Finishing
- Material Type: Different metals and plastics respond uniquely to bead blasting, so choose accordingly.
- Surface Complexity: Intricate designs might require specialized techniques or equipment for even finishes.
- Desired Finish: Determine if you want a rough texture, matte appearance, or a specific level of smoothness.
- Post-Blasting Treatments: Consider subsequent processes like painting or anodizing; bead blasting can prep surfaces for better adhesion.
- Component Function: Ensure the finish doesn't hinder the part's intended function or fit.
- Safety Protocols: Ensure designs allow for safe and efficient bead blasting without risk to operators.
Other surface finishes for CNC parts
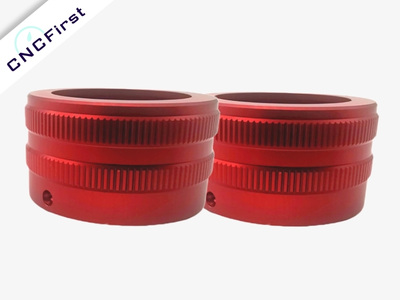
Anodizing is a process that can be suitable for CNC machined parts to enhance their performance, appearance and durability. It immerses the part in an electrolyte bath and applying an electric current which helps create a protective oxide film on its surface.
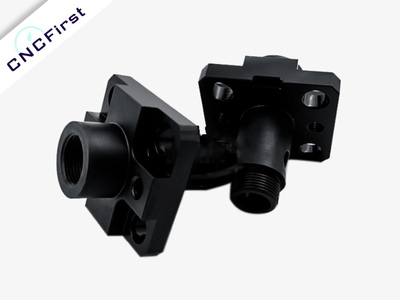
Black oxide is also referred to as blackening, and it adds a matte black finish to the metal, making the surface look darker in contrast to its original state. It makes the CNC parts appear more aesthetically pleasing while also protecting it from corrosion and rusting.
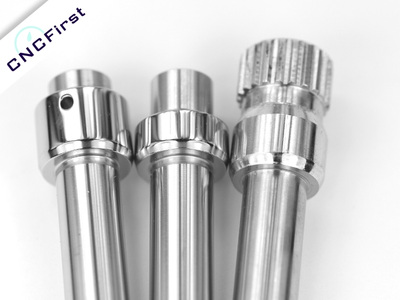
The goal of polishing is to enhance the natural beauty of the material so that it looks better than when it was first created.
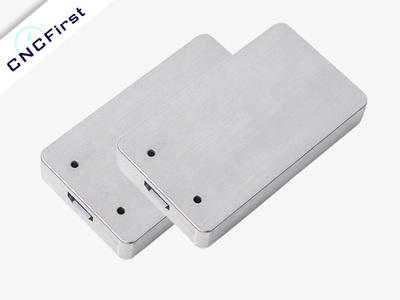
Brushing is a process that ensures the cleanliness and accuracy of a final product. This involves using wire brushes to remove metal burrs, shavings and any other contaminants from the surface of the part.
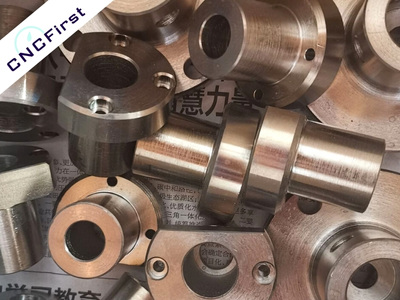
Electroless nickel plating
Electroless nickel plating is an incredibly useful process for adding a protective layer of metal to a variety of surfaces. It involves immersing the object in an electroless nickel solution, which then deposits nickel onto the surface.
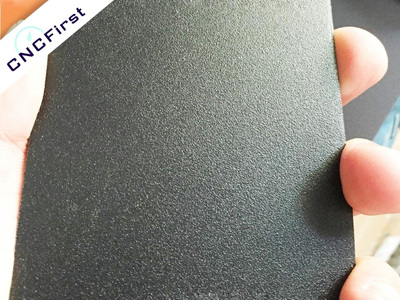
Powder coating uses a fine powder that is electrostatically charged and then sprayed onto the desired product. It finally forms an incredibly durable finish that can withstand harsh weather conditions, corrosion, chemicals and abrasion far better than traditional wet paint.
Bead Blasting FAQs
What differentiates bead blasting from sandblasting?
Bead blasting and sandblasting are abrasive, but they serve different purposes. Bead blasting uses fine glass beads to give a clean, matte finish, ideal for delicate surfaces without removing the underlying material. It can refer to the process of sandblasting or abrasive blasting.
Sandblasting, on the other hand, employs coarse sand grains, which can be more aggressive, removing rust, old paint, and more significant surface imperfections.
How long does the bead blasting process take?
The duration for bead blasting largely depends on the intricacy and size of the part, as well as the desired finish. For smaller components or fewer items, it can be completed within hours. However, for larger projects or batches, it might span days. Ensuring quality over speed is crucial so each part gets the desired finish.
Is bead blasting suitable for intricately designed parts?
Absolutely! Bead blasting’s precision allows it to cater to parts with detailed designs without causing damage. The fine beads effectively reach crevices and intricate patterns, ensuring a consistent finish. However, the technician’s skill and the equipment’s calibration are vital in achieving desired outcomes for detailed parts.
What safety measures are incorporated during bead blasting?
Safety is paramount in bead blasting. Operators wear protective gear, including safety goggles, gloves, and respiratory masks, to prevent bead inhalation and skin contact. Furthermore, the process is often conducted within enclosed chambers or booths to contain the beads and prevent them from becoming a hazard in the workplace.
What are the Bead Blasting Media?
Bead blasting employs a variety of media to achieve distinct finishes.
The most common are glass beads, prized for their consistency and gentle abrasion. Ceramic beads are tougher and offer an extended lifespan. Plastic beads are softer, ideal for delicate parts that can’t tolerate aggressive media.
Other options include walnut shells and corn cobs for organic finishes. The choice of media is crucial, influencing both the finish quality and the component’s integrity. It also includes aluminum oxide and steel shot.
Applications of Metal Materials for Bead Blasting
When it comes to bead blasting, the suitability and adaptability of the process largely depend on the metal in question. Here’s a look at some metals that are prime candidates for bead blasting and why:
Aluminum: A popular choice in various industries, aluminum is lightweight and corrosion-resistant. Bead blasting aluminum parts ensures a consistent matte finish, removing surface inconsistencies and prepping it for subsequent treatments like anodizing.
Stainless Steel: Renowned for its durability and resistance to rust, stainless steel greatly benefits from bead blasting. This process effectively removes the weld discoloration, ensuring a uniform appearance while retaining its anti-corrosion properties.
Brass: Commonly used in decorative fixtures and components, brass can tarnish over time due to its golden hue. Bead blasting revives its appearance, providing a refreshed, even finish without damaging the metal’s inherent characteristics.
Titanium: As a strong yet lightweight metal, titanium is favored in aerospace and medical devices. Bead blasting titanium parts helps remove any surface contaminants and ensures an even, matte surface.
Copper: Copper, with its brilliant reddish-brown luster, can oxidize over time. Bead blasting helps restore its shine, remove oxidation layers, and prepare it for coatings to prevent future tarnish.
Request a Quote for Your Bead Blasting Needs
Ready to elevate the finish of your components? Connect with our bead blasting experts to discuss your project’s specifics. Our team is on standby to provide tailored solutions and competitive quotes. Don’t wait; reach out today and let us transform your CNC parts. Contact us now!