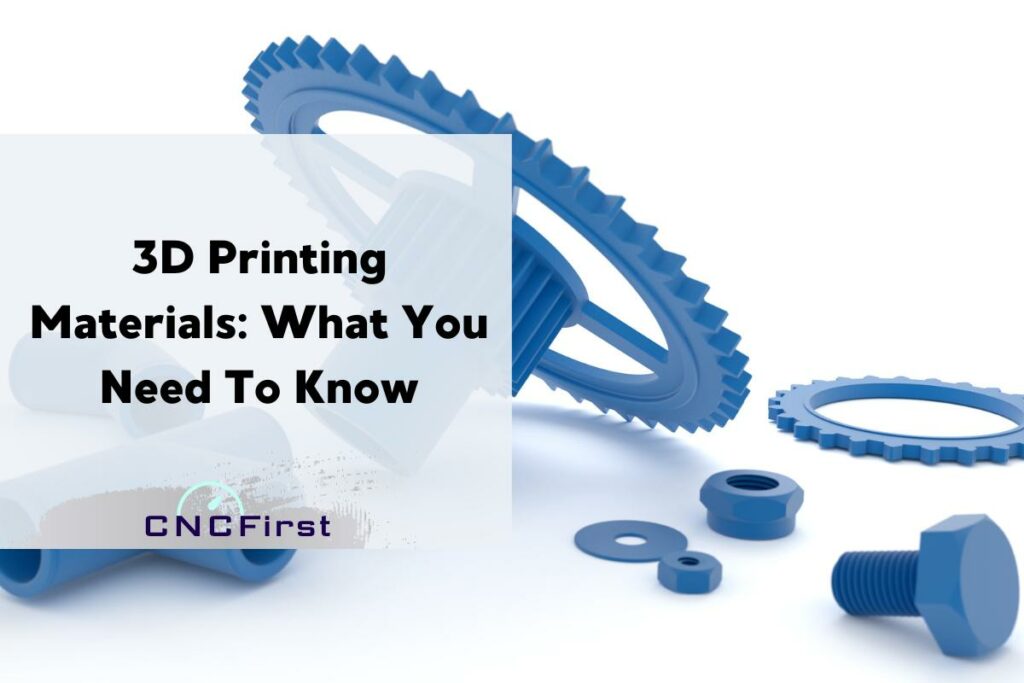
3D printing has revolutionized the way we create and manufacture objects. From prototypes to customized products, this technology has opened up a world of possibilities. But one key factor that determines the quality and functionality of 3D printed objects is the 3d printing materials used.
In this blog post, we’ll dive into the world of 3D printing materials and explore everything you need to know. From PLA to ABS and beyond, we’ll discuss the different types of materials available, their properties, and their applications.
So whether you’re new to 3D printing or looking to expand your knowledge, this blog post is a must-read. Get ready to uncover the secrets behind successful 3D printing!
Types of 3D Printing Materials
When it comes to 3D printing, materials play a pivotal role in determining the quality, strength, and suitability of the final product. Let’s delve into the various types of materials commonly used for 3d printing:
Plastics:
Plastics are among the most widely materials in 3D printing due to their versatility and affordability. Some common plastic materials include:
PLA (Polylactic Acid): PLA is a biodegradable thermoplastic derived from renewable resources like corn starch or sugarcane. It is popular for its ease of use, low warping, and wide range of available colors.
ABS (Acrylonitrile Butadiene Styrene): ABS is a durable thermoplastic known for its strength and impact resistance. It is commonly used in applications requiring toughness and heat resistance, such as automotive parts and consumer goods.
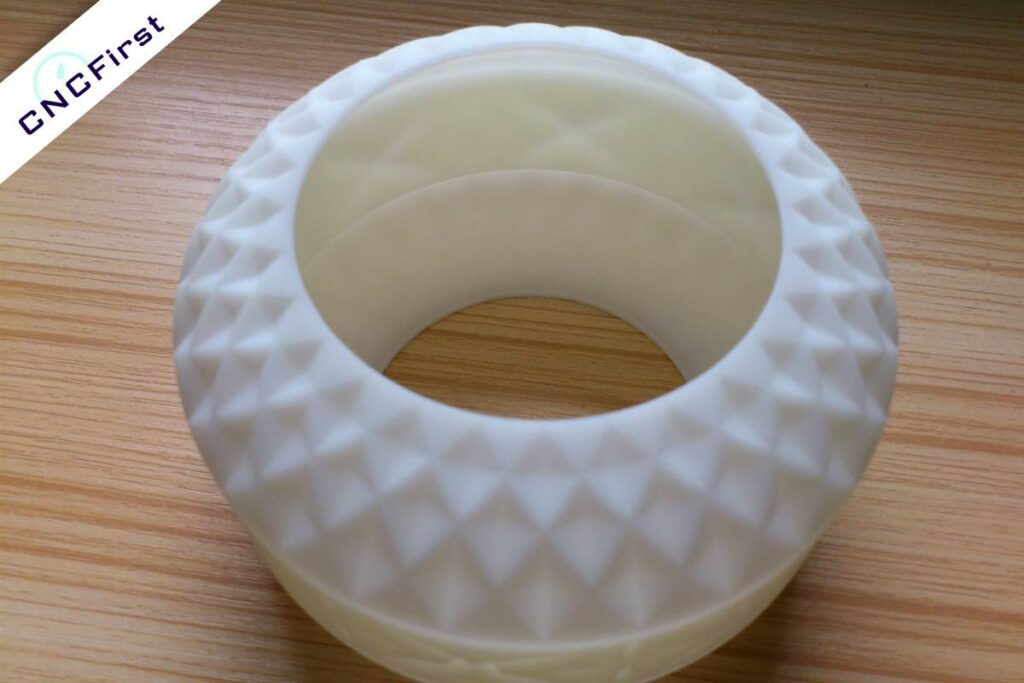
PETG (Polyethylene Terephthalate Glycol): PETG is a transparent thermoplastic known for its excellent layer adhesion and impact resistance. It offers a balance of strength and flexibility, making it suitable for a variety of functional prototypes and end-use parts.
Nylon: Nylon, also known as polyamide, is a strong and flexible thermoplastic with high impact resistance and excellent layer bonding. It is commonly suitable for engineering applications where durability and toughness are essential, such as gears, bearings, and structural components.
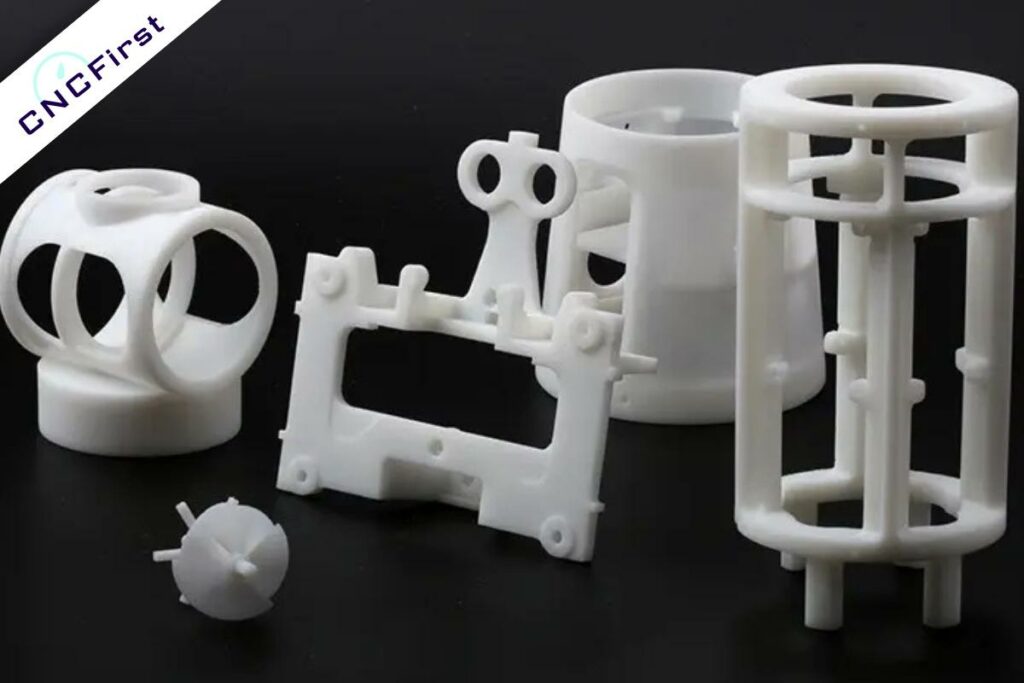
Each type of plastic offers unique properties and advantages, allowing for a wide range of applications in 3D printing.
Metals:
In the realm of 3D printing, metals offer unparalleled strength and durability, making them ideal for a variety of applications. Here are some common metal materials:

Stainless Steel: Renowned for its corrosion resistance and mechanical properties, stainless steel is a popular choice for 3D printing in industries such as aerospace, automotive, and healthcare.
Aluminum: With its lightweight yet robust characteristics, aluminum is widely suitable for 3D printing for aerospace components, automotive parts, and consumer electronics due to its excellent thermal conductivity and machinability. Also, aluminum is widely suitable for CNC machining.
Titanium: Known for its exceptional strength-to-weight ratio and biocompatibility, titanium is a preferred material for medical implants, aerospace components, and high-performance engineering applications.
Copper: Copper boasts excellent electrical conductivity and thermal conductivity, making it a favored material for 3D printing electrical components, heat exchangers, and intricate decorative pieces.
Transitioning from plastics to metals opens up new possibilities for engineering complex and high-performance parts in 3D printing.
Resins:
Resins are gaining popularity in 3D printing for their ability to produce highly detailed and precise parts. Here are some noteworthy resin materials:
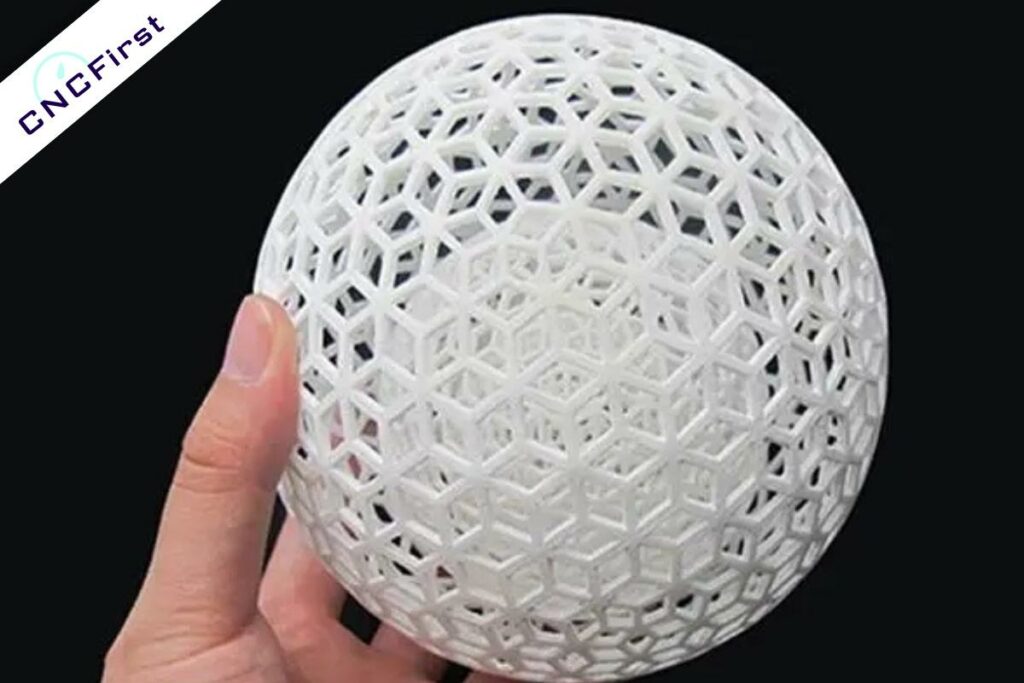
Standard Resins: Standard resins are versatile materials suitable for a wide range of applications. They offer high-resolution and smooth surface finishes, making them ideal for prototyping, jewelry making, and dental models.
Tough and Durable Resins: Tough and durable resins are engineered to withstand mechanical stress and impact, making them suitable for functional prototypes, manufacturing tools, and end-use parts requiring strength and resilience.
Flexible Resins: Flexible resins exhibit elasticity and stretchability, allowing for the creation of rubber-like parts with varying degrees of flexibility. These resins find applications in prototyping, soft robotics, and wearable devices.
Castable Resins: Castable resins are formulated to burn out cleanly during the investment casting process, leaving behind high-resolution metal parts. They are commonly used in jewelry making, dental prosthetics, and custom metal components.
Transitioning to resins in 3D printing expands the possibilities for creating intricate and functional parts with diverse mechanical properties.
Ceramics:
Ceramics opens up a world of possibilities for creating parts with exceptional thermal and chemical resistance, making them suitable for high-temperature applications in industries such as aerospace, automotive, and electronics.
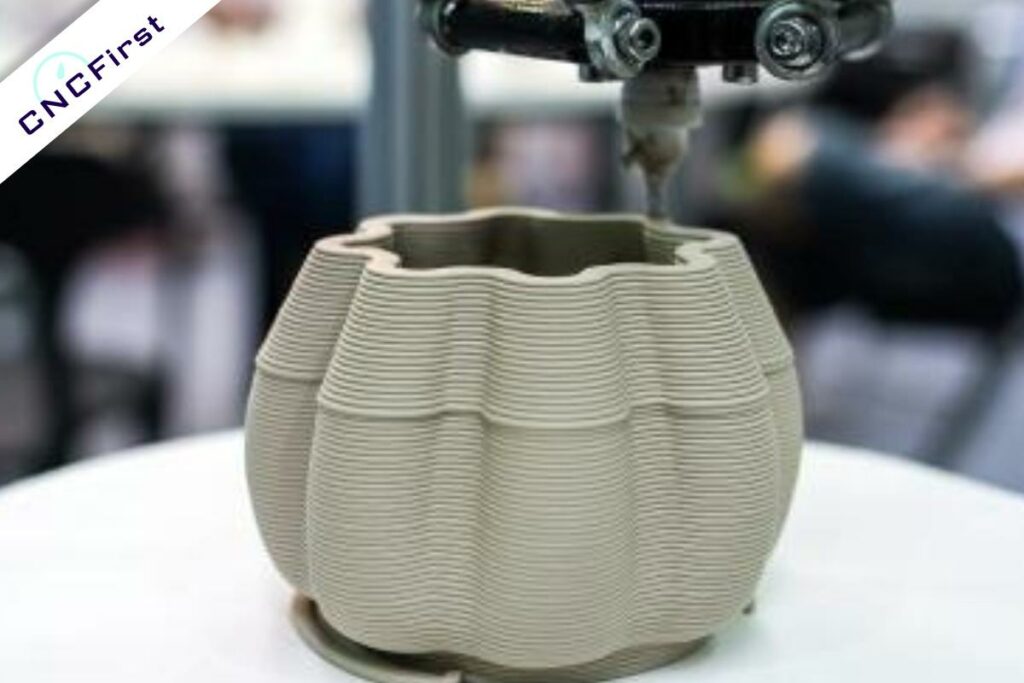
Porcelain: Porcelain is a versatile ceramic material known for its hardness, durability, and smooth surface finish. It is commonly used in dental restorations, tableware, and decorative objects due to its aesthetic appeal and biocompatibility.
Alumina: Alumina, also known as aluminum oxide, is a high-performance ceramic material with excellent mechanical strength, electrical insulation, and corrosion resistance. It finds applications in aerospace components, electronic substrates, and medical implants.
Zirconia: Zirconia, or zirconium dioxide, is a bioinert ceramic material prized for its exceptional strength, biocompatibility, and tooth-like aesthetics. It is widely used in dental crowns, implants, and prosthetics due to its durability and natural appearance.
Silica: Silica, or silicon dioxide, is a versatile ceramic material with high thermal stability and low thermal expansion. It is suitable for various applications such as refractories, glassmaking, and semiconductor manufacturing due to its excellent optical, mechanical, and electrical properties.
Composites:
Composites offer a unique combination of strength, lightweight, and versatility, making them suitable for a wide range of applications. Here are some notable composite materials:
Carbon Fiber: Carbon fiber composites are renowned for their exceptional strength-to-weight ratio and stiffness, making them ideal for aerospace, automotive, and sporting goods applications requiring lightweight and high-performance materials.
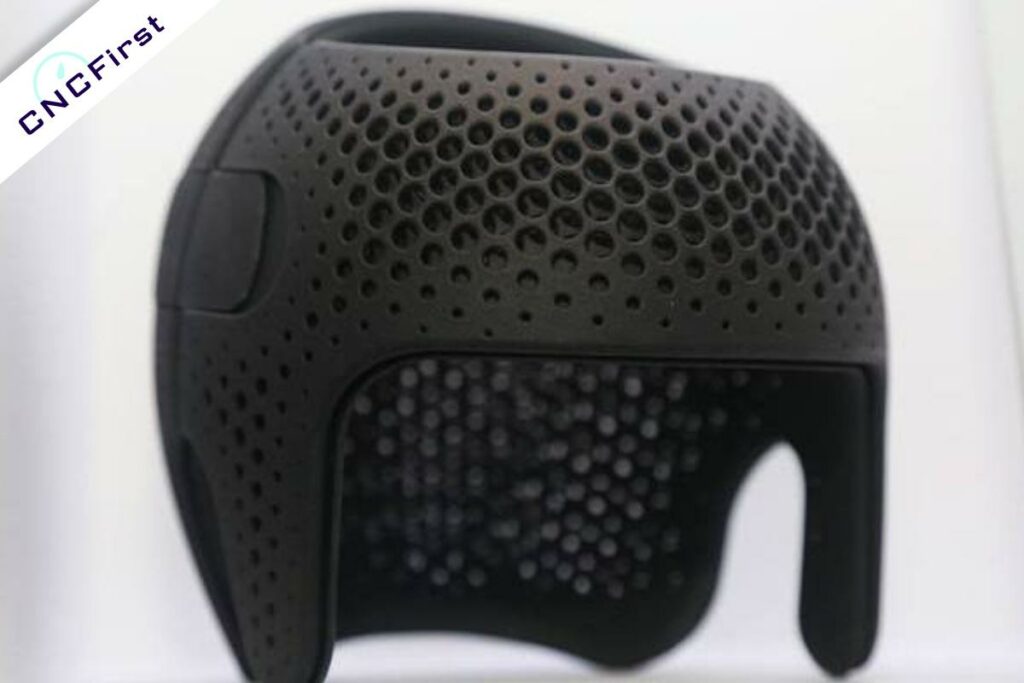
Fiberglass: Fiberglass composites consist of glass fibers embedded in a resin matrix, offering excellent strength, durability, and corrosion resistance. They find applications in marine, construction, and automotive industries due to their versatility and cost-effectiveness.
Kevlar: Kevlar composites are known for their outstanding tensile strength, heat resistance, and impact resistance. They are commonly used in ballistic armor, aerospace components, and sporting equipment for their ability to provide superior protection and durability.
Types of Plastic 3D Printing Processes
FDM 3D Printing
Fused Deposition Modeling (FDM) is a popular 3D printing technique that extrudes thermoplastic filaments layer by layer to build up the desired object. This process offers affordability, simplicity, and a wide range of material options, making it suitable for rapid prototyping, hobbyist projects, and low-volume production.
SLA 3D Printing
Stereolithography (SLA) 3D printing utilizes a vat of liquid photopolymer resin and a UV laser to selectively cure the resin layer by layer, resulting in highly detailed and precise parts. SLA is favored for its high-resolution capabilities, smooth surface finishes, and suitability for producing intricate prototypes, jewelry, and dental models.
SLS 3D Printing
Selective Laser Sintering (SLS) is a powder-based 3D printing process that uses a high-power laser to selectively fuse powdered thermoplastic materials, such as nylon, into solid parts layer by layer. SLS offers design freedom, material versatility, and the ability to produce complex geometries without the need for support structures, making it ideal for functional prototypes, end-use parts, and customized production components.
From FDM to SLA and SLS the possibilities for creating high-quality plastic parts with varying levels of detail, precision, and mechanical properties, catering to a wide range of industrial and consumer applications.
check stampa3dstore for more information
Metal 3D Printing Process
3D printers use a process called direct metal laser sintering to create 3D printed parts out of metal powder. This method is becoming increasingly popular due to its low cost and the wide range of 3D printing materials available.
Unlike traditional 3D printing using plastic filament, metal 3D printing involves melting metal dust with a laser to create solid objects. Some of the most common materials for 3D printing include various types of plastic and materials that can be used as support material. Metal is considered one of the strongest materials that can be used in 3D printing.
Factors to Consider When Choosing 3D Printing Materials
When selecting 3D printing materials, several crucial factors must be taken into account to ensure the desired performance and suitability for the intended application. Here are the key considerations:
Strength and Durability Requirements: The strength and durability of the material should align with the demands of the application. Consider factors such as mechanical stress, impact resistance, and load-bearing capacity to determine the optimal material choice.
Heat Resistance: Evaluate the material’s ability to withstand high temperatures without deforming or losing structural integrity. This is particularly important for applications exposed to elevated temperatures or thermal cycling.
Chemical Resistance: Determine if the material can resist exposure to chemicals, solvents, or corrosive substances commonly encountered in the application environment. Chemical resistance ensures the longevity and reliability of the printed parts.
Flexibility and Elasticity: Depending on the intended use, consider the material’s flexibility and elasticity. Flexible materials are suitable for applications requiring resilience and deformation resistance, while rigid materials offer stability and structural support.
Surface Finish and Post-Processing Capabilities: Assess the surface finish achievable with the chosen material and the feasibility of post-processing techniques such as sanding, polishing, or painting to meet aesthetic or functional requirements.
Cost Considerations: Balance the performance requirements with the cost of the material, including raw material expenses, printing consumables, and post-processing costs. Optimize material selection to achieve the desired outcome within budget constraints.
By carefully evaluating these factors, designers and engineers can make informed decisions when choosing 3D printing materials, ensuring optimal performance, functionality, and cost-effectiveness for their projects.
Conclusion
Choosing the right material is crucial when it comes to 3D printing. The material you select will determine the strength, durability, and overall quality of your printed objects.
Whether you need a flexible material for intricate designs or a strong and heat-resistant material for functional parts, there is a material out there that will suit your needs.
By understanding the characteristics of each material and its applications, you can make informed decisions when it comes to selecting the right material for your 3D printing projects.
So go ahead and experiment with different materials to unlock the full potential of 3D printing technology!