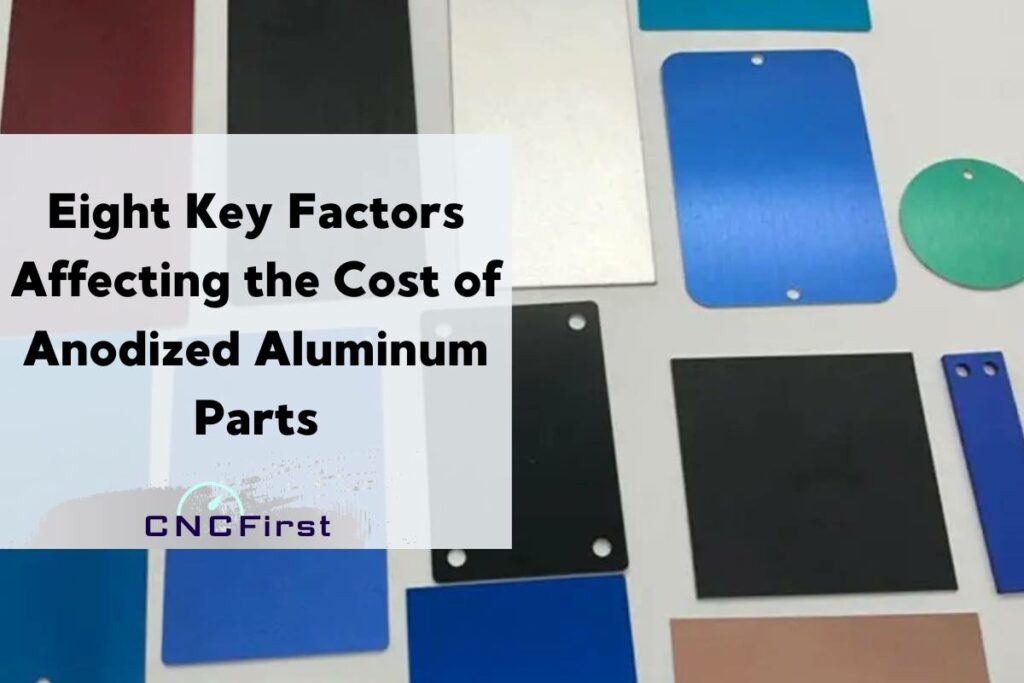
Anodizing, a crucial electrolytic process, transforms the surface of aluminum parts into a durable, corrosion-resistant finish. This protective layer not only enhances the lifespan of the aluminum but also boosts its aesthetic appeal. However, the cost of anodized aluminum isn’t static. It varies considerably based on several factors, making it essential for businesses and individuals to grasp what drives these fluctuations.
This post aims to delve into the intricacies of the anodizing process, shed light on its significance, and elucidate the elements that influence its cost. Understanding these variables enables one to make informed decisions when budgeting for anodizing services.
What is Aluminum Anodizing?
Aluminum anodizing is a transformative process that enhances the metal’s durability, resistance to corrosion, and aesthetic appeal. By immersing aluminum in an electrolytic solution and applying an electric current, a protective oxide layer forms on the metal’s surface.
This layer not only fortifies the aluminum but also serves as a base for various finishes, including a spectrum of anodized aluminum colors.
For the best surface finish for aluminum parts, many people prefer anodizing to painting. The result is a combination of enhanced physical properties and a visually appealing finish, making anodized aluminum a preferred choice for numerous applications across industries.
Eight Factors Affecting the Cost of Anodize Aluminum Parts
1. Material and Size of Aluminum Parts
The type of aluminum used plays a pivotal role in determining the cost of the anodized aluminum. For instance, the popular 6061 alloy, known for its strength and versatility, might have a different anodizing cost compared to other aluminum alloys. The reason? Each aluminum type possesses unique properties, affecting the anodization quality and the resources required.
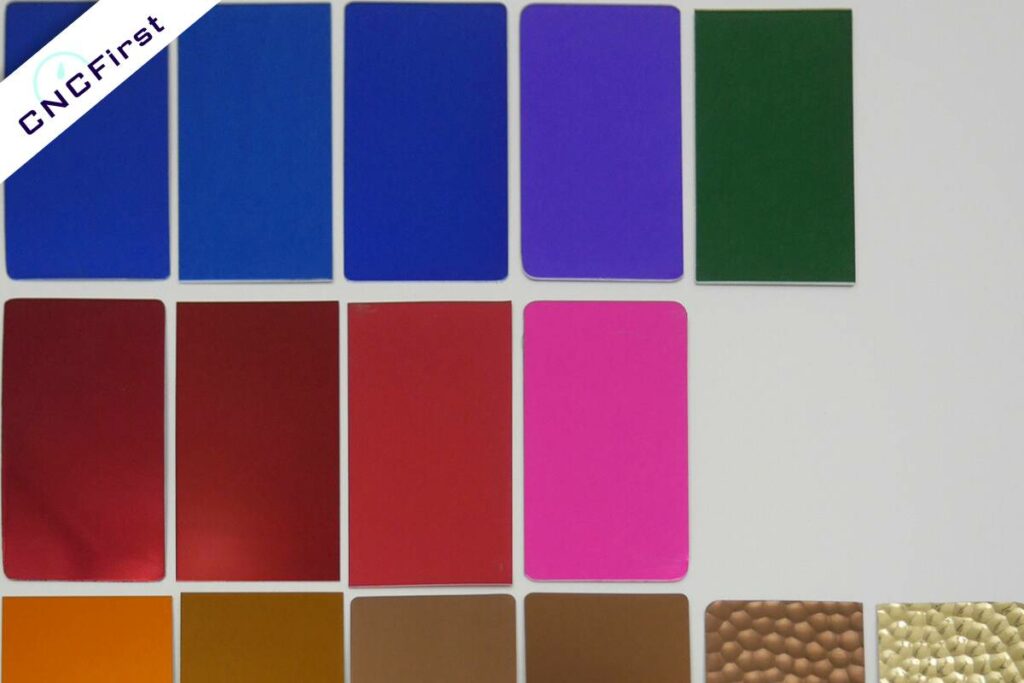
Furthermore, the size of the aluminum part is another significant cost influencer. Anodizing services often employ a rule of thumb based on square inches. Essentially, the larger the surface area, the more materials and time are needed, leading to a higher cost.
Conversely, smaller parts might cost less in terms of raw materials but could have higher per-piece charges due to the intricacies of handling and processing. In essence, both the material type and size are paramount when estimating anodizing expenses.
2. Type of Anodizing Process
The anodizing world isn’t one-size-fits-all. Different projects demand various anodizing types, each with its unique characteristics and cost implications. Type II anodizing, often referred to as “sulfuric acid anodizing,” is the most common method. It produces a thin, clear layer that can be dyed to achieve various colors. However, other types, like Type III or “hard anodizing,” result in a thicker, more wear-resistant finish, often at a higher cost.
The desired finish also plays a role in the pricing equation. For instance, black anodizing, a sought-after finish for its sleek appearance, might come with a premium price tag due to the specific dyes and processes required. In contrast, natural or clear anodized finishes might be more cost-effective. It’s essential to understand that choosing the anodizing type and finish directly correlates with the final cost, making it a critical consideration in the decision-making process.
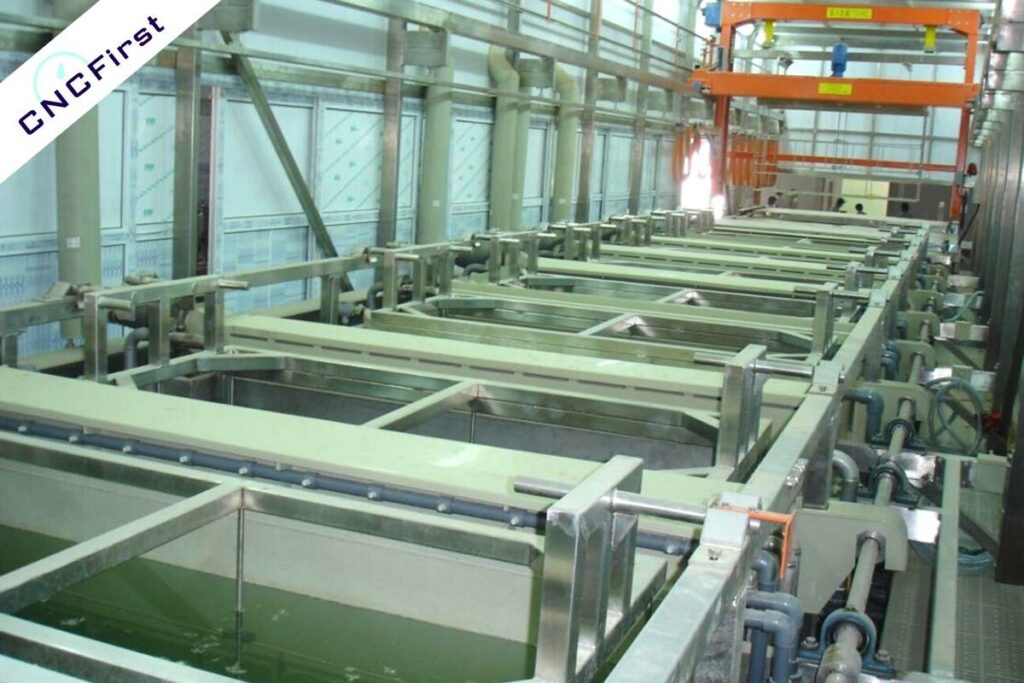
3. Coating Thickness
Coating thickness is a crucial factor that affects the cost of anodized aluminum parts. The thickness of the coating directly impacts the amount of anodizing solution, time, and labor required in the process. A thicker coating requires more resources, leading to higher costs.
Additionally, a thicker coating may result in a more durable and long-lasting finish, which could justify the higher price for certain applications. However, for projects with budget constraints, opting for a thinner coating can be a cost-effective solution while still achieving the desired level of protection and aesthetics.
4. Minimum Lot Charges
In the realm of anodizing, it’s not just the process or material that dictates the cost; the concept of lot charges also comes into play. Essentially, minimum lot charges are the base fees that anodizing services impose, regardless of the size or number of parts in a batch. This means that even if you’re anodizing a small quantity, you might still be billed a set minimum fee.
The implications of these charges become more evident when we consider quantity. For larger batches, the lot charge gets distributed across more pieces, effectively reducing the cost per piece. On the other hand, for smaller batches, the lot charge might constitute a significant portion of the overall cost, making the per-piece expense relatively higher. It’s a delicate balance of quantity versus cost, emphasizing the importance of understanding lot charges when budgeting for anodizing projects.
5. Quality and Consistency
In the anodizing industry, quality isn’t just a buzzword—it’s a fundamental requirement. A high-quality anodized finish ensures durability, aesthetic appeal, and resistance to wear and corrosion. However, achieving such a finish often demands meticulous attention to detail and the use of premium resources, which can elevate costs.
Consistency, too, is paramount. Inconsistent anodizing can lead to undesirable outcomes like blotchy appearances or uneven finishes. These issues not only compromise the visual appeal but also the functional attributes of the anodized layer. Addressing such inconsistencies often means reworking or even discarding affected parts, leading to increased expenses.
In essence, while opting for top-notch quality and consistency might come with a higher initial price tag, it’s a worthy investment. Cutting corners might seem cost-effective in the short run but can lead to more significant expenses and reputational damage in the long haul.
6. Labor and Racking Costs
Behind every impeccable anodized finish lies the hard work of skilled professionals. Labor costs, therefore, form a significant chunk of the anodizing expense. The expertise required, the time taken for the process, and the prevailing wage rates in a region all contribute to the labor charges. As with many industries, higher expertise often equates to higher costs, but it’s a trade-off for quality assurance.
Racking, the method by which aluminum parts are held during the anodizing process, also has cost implications. Different parts require specific racking techniques to ensure even anodization and prevent damage. Some methods are more time-consuming or require specialized equipment, leading to increased costs. Moreover, the racking process can influence the amount of usable surface area, with inefficient racking potentially wasting valuable space and resources.
In summary, both labor expertise and the chosen racking method play pivotal roles in shaping the final anodizing bill.
7. Geographic Location and Competition
Geography plays a surprisingly influential role in the cost of anodized aluminum. In regions with higher living standards or operational costs, anodizing services might charge more to cover their expenses. Conversely, in areas where these costs are lower, more competitive pricing might be observed.
Competition further complicates the pricing landscape. In locales saturated with anodizing services, providers might offer competitive rates to attract clientele. However, in areas with limited service providers, prices could be higher due to the lack of alternatives. Essentially, the interplay between geographic location and the density of competitors can significantly sway the cost dynamics of anodizing.
8. Special Requirements
Every anodizing project is unique, and sometimes, specific requirements can add to the cost. For instance, masking, a process used to protect certain areas from anodizing, demands additional labor and materials, leading to a price uptick. Similarly, if a project requires mixed types of powder coating or specialized finishes, the complexity increases, and so does the cost.
These bespoke requirements, while enhancing the final product’s quality and appeal, necessitate specialized skills and resources. As a result, while they ensure a tailored outcome, they also come with a premium, underscoring the importance of clear communication and budgeting when seeking specialized anodizing services.
Tips to Enhance Anodizing
Aluminum anodizing is an electrochemical process that involves coating an aluminum surface with a wear-resistant oxide layer. Achieving a flawless anodized finish requires more than just understanding the process. It’s about mastering the nuances and implementing best practices to ensure consistent, high-quality results. Here are some invaluable tips to elevate your anodizing game:
Material Selection: Opt for high-quality aluminum alloys. The purer the metal, the more uniform the anodized layer will be.
Pre-treatment: Ensure thorough cleaning of the aluminum surface. Removing oils, dirt, and contaminants is crucial for an even finish.
Consistent Current: Maintain a steady electric current during the anodizing process. Fluctuations can lead to uneven oxide layers.
Temperature Control: Monitor the electrolytic solution’s temperature. A consistent temperature ensures a uniform anodized layer.
Dye Quality: If adding color, use high-quality dyes. Premium dyes result in vibrant, long-lasting hues.
Sealing: After anodizing, seal the aluminum properly. This step locks in the color and enhances the layer’s resistance to wear and corrosion.
Routine Maintenance: Regularly inspect and maintain your anodizing equipment. Clean tanks, replace worn-out components and ensure all parts are functioning optimally.
By adhering to these tips and maintaining a keen eye for detail, you can consistently achieve impeccable anodized finishes that stand the test of time.
Conclusion
Anodizing aluminum is a multifaceted process, with costs influenced by a myriad of factors ranging from the type of aluminum and desired finish to geographic location and special requirements.
Grasping these determinants is paramount, as it not only aids in making informed decisions but also ensures optimal budget allocation.
By understanding the nuances of each cost-driving element, businesses and individuals can navigate the anodizing landscape more effectively, striking a balance between quality and cost. In essence, a comprehensive knowledge of these factors is the cornerstone of successful, cost-effective anodizing endeavors.
Choose CNCFRIST for Premium Anodizing Services!
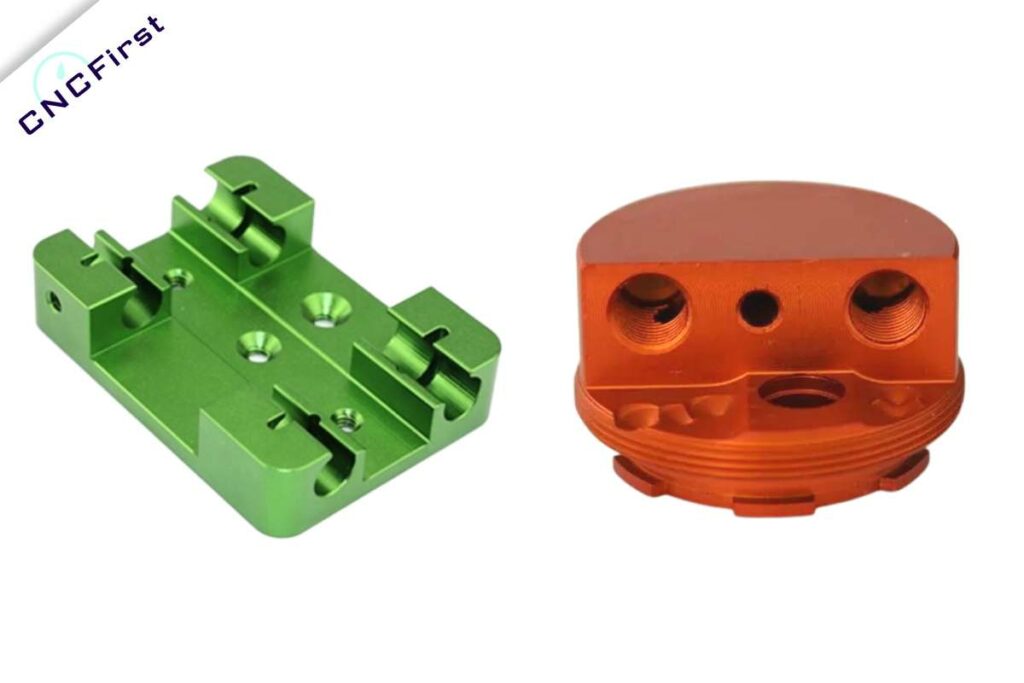
When it comes to anodizing, don’t settle for anything less than the best. At CNCFRIST, we combine expertise with cutting-edge technology to deliver impeccable surface finishes every time. Whether you’re seeking vibrant colors or a durable protective layer, our team is equipped to exceed your expectations. Ready to elevate your aluminum products? Trust the experts. Contact CNCFRIST today and discover the difference of top-tier anodizing services. Your aluminum deserves the best, and we’re here to provide it. Reach out now!
FAQs
How is the cost of anodizing typically calculated?
The cost of anodized aluminum is often determined by multiple factors, including the type and size of the aluminum, the desired finish, labor costs, and any special requirements. Additionally, the surface area to be anodized, usually measured in square inches, plays a significant role in the pricing.
Does the color of the anodized finish affect the cost?
Yes, the color can influence the cost of anodized aluminum. While natural or clear finishes might be more economical, specific colors, especially unique or vibrant ones like black, may require specialized dyes and processes, leading to a higher price point.
How do minimum lot charges work?
Minimum lot charges are base fees imposed by anodizing services, irrespective of the batch size. This means even if you’re anodizing a small quantity, you might still incur a set minimum fee. For larger batches, this charge gets distributed across more pieces, reducing the cost per item.
Can the quality of the aluminum material affect the anodizing cost?
Absolutely. The quality of the aluminum can impact the anodizing process’s efficiency and the finish’s consistency. Premium-grade aluminum might yield better results but could come at a higher cost, while lower-quality materials might pose challenges, potentially increasing labor and resource costs.
Are there ways to reduce the cost of anodizing?
Certainly! Opting for bulk anodizing, choosing standard finishes over specialized ones, and sourcing services from regions with competitive pricing can help reduce costs. Additionally, maintaining a consistent quality of aluminum parts can prevent reworks, further saving on expenses.