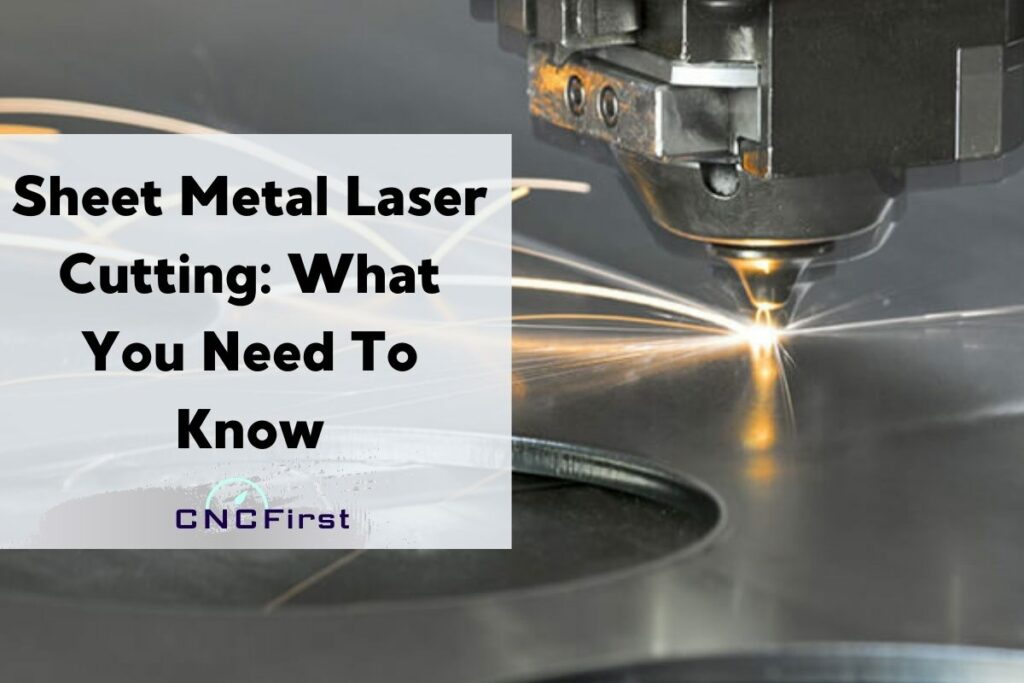
Sheet metal fabrication is versatile in various applications, but sheet metal laser cutting can be difficult and time-consuming.
Sheet metal laser cutting is the perfect solution for quickly and easily cutting sheet metal. Our laser cutters can make clean and precise cuts with little effort.
This blog will have our sheet metal cutting expert take us through laser cutting.
What Is Laser Cutting And Its Operating Principle
Sheet metal laser cutting is a process that uses a laser to cut materials like aluminum, stainless steel, and carbon steel.
The laser beam melts the material as it cuts through it, and the speed and precision of the laser make it ideal for cutting sheet metal.
Three things happen when sheet metal is cut with a laser: the material is melted, vaporized, and blown away.
The laser beam has a very high energy density so that it can heat the material quickly. This causes the material to melt and vaporize. The high pressure of the laser also blows away the material that has been vaporized, leaving a clean-cut edge.
Why Is Laser Cutting a Good Fit For Sheet Metal Fabrication?
Many people think of lasers as tools for cutting hard materials, but they can also be used to cut softer materials like sheet metal.
- Laser cutting is an excellent fit for sheet metal fabrication for some reasons:
- Laser cutting is very precise, so it can produce tight tolerances and clean edges.
- Lasers can cut quickly, which can be a significant advantage when working on large projects.
- Lasers create very little waste since the material is vaporized as it is cut.
- It also can cut various metals, including stainless steel and aluminum.
As a result, laser cutting is a versatile and efficient option for sheet metal fabrication.
Types Of Laser For Sheet Metal Cutting
There are three prime types of laser cutting: laser beam fusion cutting, laser beam flame cutting, and laser beam sublimation cutting—each with its advantages and disadvantages.
Laser Beam Fusion Cutting
Laser beam fusion cutting is the most common type of laser cutting. It uses a high-powered laser to melt the metal, which is then blown away by a gas jet. This method is exact and can be used on various metals. However, it is also the most expensive.
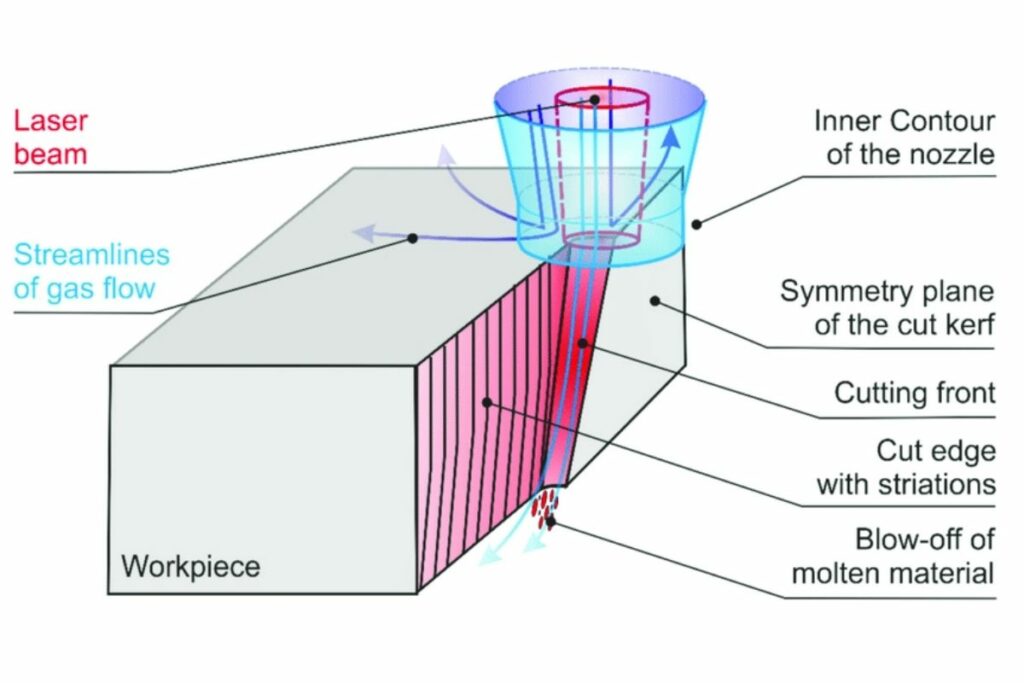
Laser Beam Flame Cutting
Laser beam flame cutting is less precise than fusion cutting but is much cheaper. This method uses a lower-powered laser to heat the metal until it ignites. The burning metal is then blown away by a jet of gas. While this method can be used on thinner metal sheets, it is unsuitable for all metals.
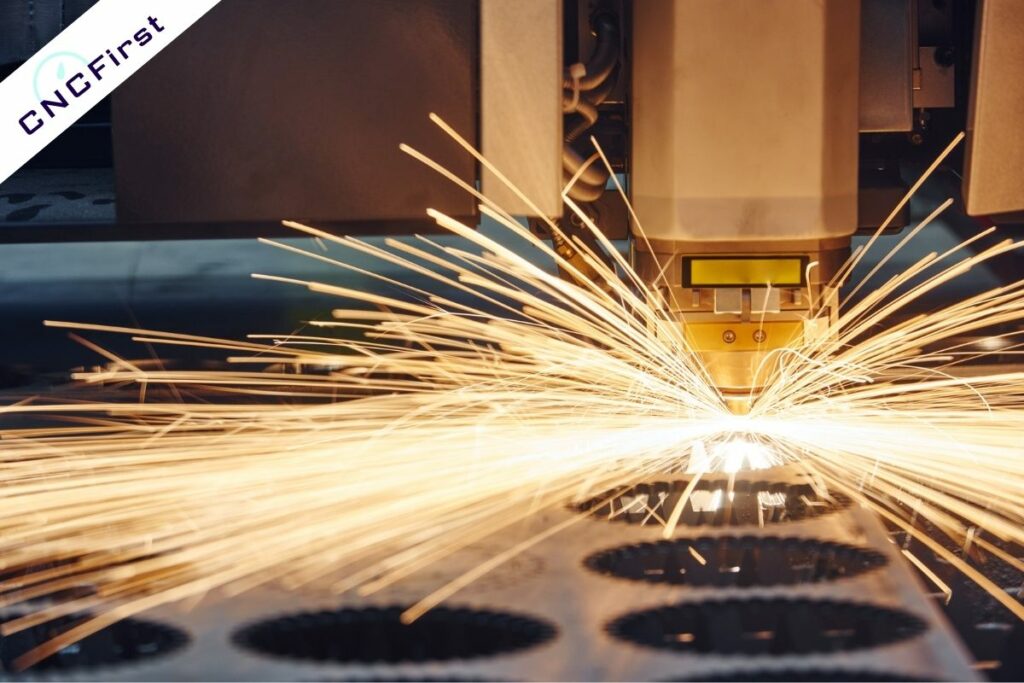
Laser Beam Sublimation Cutting
Laser beam sublimation cutting is the least common type of laser cutting. In this method, a high-powered laser vaporizes the metal, which is then blown away by a gas jet. This method is exact but can only be used on certain metals. It is also the most expensive type of laser cutting.
Three Sheet Metal Laser Cutting Processes
The three most common laser cutting processes are CO2, fiber, and disk. Each process has advantages and disadvantages, so choosing the right one for your project is essential.
Co2 Laser Cutting
CO2 laser cutting is the most popular process for cutting sheet metal. It’s inexpensive and can be used on a variety of materials. However, it doesn’t work well on thick or reflective materials.
Fiber Laser Cutting
Fiber laser cutting is a newer technology that’s become very popular recently. It’s more expensive than CO2 laser cutting, but it can cut thicker materials and reflects less light, making it ideal for projects that require precision cuts.
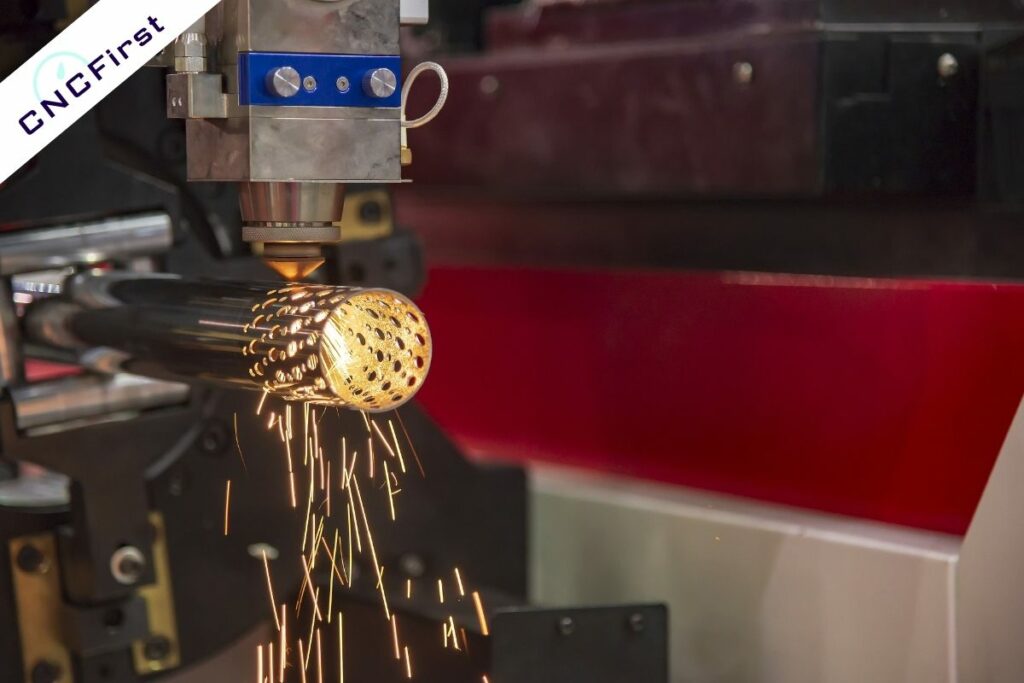
Disk Laser Cutting
Disk laser cutting is the most expensive of the three processes, but it offers the best precision and can cut through the thickest materials. If you need to make intricate cuts or cut large sheets of metal, disk laser cutting is the best option.
Advantages Of Sheet Metal Laser Cutting
The process offers many advantages over other metal-cutting methods.
Some advantages include the following:
- Reduced set-up time because there is no need for tooling or fixturing
- Increased precision because the laser beam will not wander
- Higher speeds since the laser can cut through material very quickly
- The ability to cut complex shapes because there is no need for tooling
- Reduced labor costs because one operator can oversee multiple machines
- The ability to cut thicker materials than other methods, such as waterjet or plasma
- Increased safety since there are no fumes or sparks generated during the process
Disadvantages Of Sheet Metal Laser Cutting:
There are a few potential disadvantages to consider when considering sheet metal laser cutting.
- The initial investment in a laser cutter can be significant.
- Laser cutters require regular maintenance and calibration to ensure accuracy, which can add to the overall cost of ownership.
- Laser cutting produces large amounts of heat, distorting or damaging delicate materials.
However, laser cutting can be an exact and efficient way to cut sheet metal when appropriately used.
When weighing the pros and cons, consider specific applications to determine if laser cutting is the right choice.
Common Types of Laser Cutting Metal Materials
The most common metal materials that can be cut using laser cutting technology include stainless steel, aluminum, carbon steel, brass, and copper. Stainless steel is known for its durability and resistance to corrosion and is often used in industrial and medical applications.
On the other hand, aluminum is a lightweight and versatile metal commonly used in the aerospace and automotive industries.
Carbon steel is a cost-effective option often used in construction and machinery.
Brass and copper are softer materials often used for decorative and artistic purposes. Each material has unique properties and characteristics, making selecting the right material for your specific project essential.
7 Things To Consider in Using Sheet Metal Laser Cutting
When considering using sheet metal laser cutting for your project, there are some important things to remember. Here are some factors to consider:
Material type: Different laser cutting machines perform better on certain types of metal. Make sure to choose the right machine for your material.
Thickness: Laser cutting abilities differ based on the thickness of the sheet metal. Check the machine’s capabilities before proceeding.
Design complexity: Intricate designs may require more time and effort to cut, so account for this in your project timeline.
Finishing: Consider if the finished product requires additional finishing, such as sanding or painting.
Budget: Laser cutting can be expensive, so factor in the cost when planning your project.
Accuracy: Laser cutting is highly precise, but it’s important to ensure your design is thoroughly prepared before cutting to avoid errors.
Lead times: Laser cutting services may require lead times, so factor in the time required to cut and ship to meet your deadlines.
Our Sheet Metal Laser Cutting Capabilities
As a full-service metal fabrication company, we offer a range of services to meet the needs of our clients. One of our most popular services is state-of-the-art laser cutting. Our powerful laser cutter can cut through even the thickest metal sheets with ease, and the precision of the cuts is unmatched.
We also offer CNC plasma cutting, waterjet cutting, and more. Our skilled fabricators have years of experience working with all types of metals and can meet your specific needs with flying colors. Contact us today to learn more about our laser-cutting services.
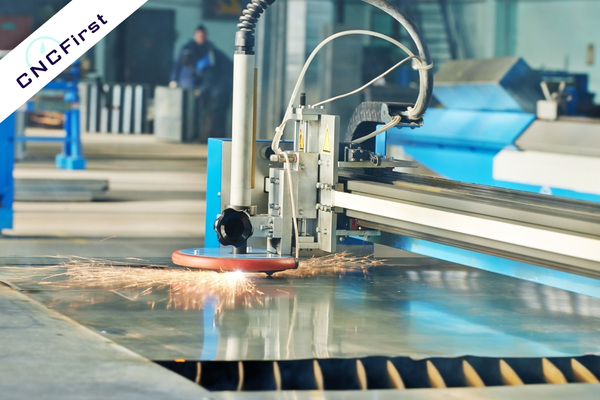
Summary
Laser-cutting technology has revolutionized the way sheet metal is cut. It offers several advantages reducing set-up time and higher speed over traditional methods, such as shearing and punching. Try a laser cutter if you are in the market for a new sheet metal cutter.
FAQs
A few common questions come up regarding laser cutting. Here are a few of the most frequently asked questions, along with their answers:
Laser Cutting: Historical Background
The history of sheet metal laser cutting can be traced back to the early days of lasers, which were first used for industrial purposes.
In the 1960s, lasers were used for cutting and welding metals, but it wasn’t until the 1970s that they were adapted for cutting sheet metal. Robert N.
Hall developed the first sheet metal laser cutter in 1974. Since then, laser cutting has become an essential part of the manufacturing process for various industries.
Laser cutters can now easily cut through thick and exotic metals, making them an indispensable tool for companies that rely on precision manufacturing.
What Is the Difference Between Laser Cutting And Waterjet Cutting?
Laser cutting uses a high-powered laser beam to melt, burn, or vaporize material, while waterjet cutting uses a stream of high-pressure water to cut through the material. Both methods can be used to cut through sheet metal.