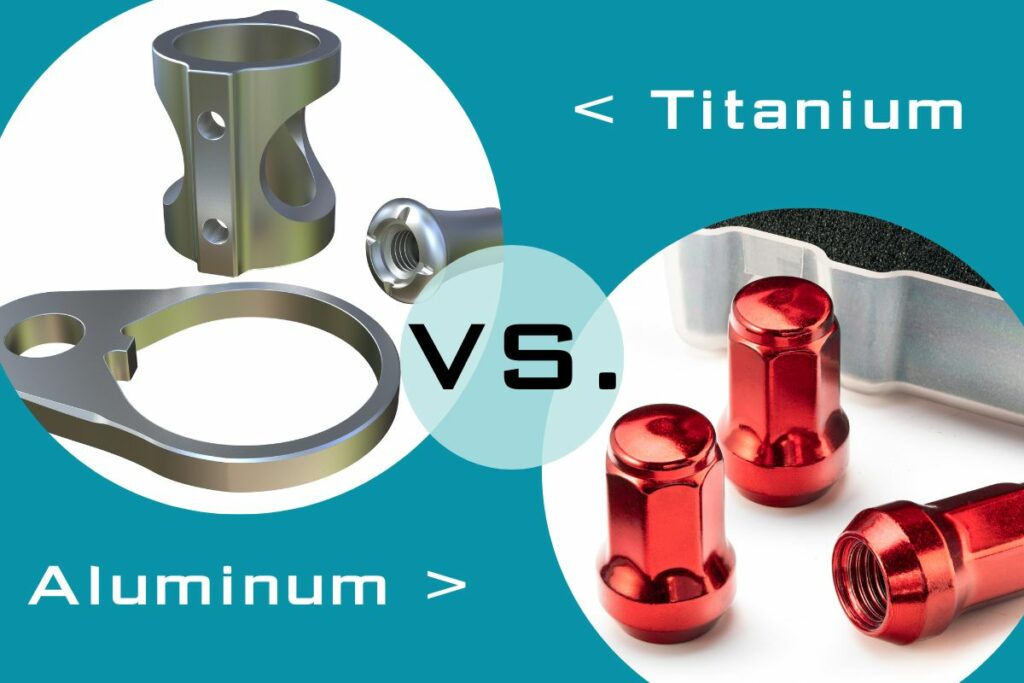
In the realm of CNC machining, where precision is paramount, the choice of materials plays a pivotal role. The delicate dance of crafting intricate components demands a thorough understanding of the properties of metals. Titanium and aluminum emerge as formidable contenders, each boasting unique characteristics. Titanium vs. aluminum in CNC Machining: what’s the difference? Which lightweight metal you should choose?
This article delves into the heart of this deliberation, exploring the properties of Titanium and Aluminum in the context of CNC machining. As we navigate through this comparison, the importance of material selection becomes apparent, influencing the outcome of precision engineering.
Join us in this exploration as we decipher the significance of choosing between Titanium and Aluminum, unraveling the intricacies that govern CNC machining processes.
Advantages of Titanium in CNC Machining
Embracing titanium in CNC machining brings forth a myriad of advantages, making it a preferred choice for various applications.
Exceptional Strength:
Titanium’s inherent strength allows for the creation of robust components without compromising on durability.
Corrosion Resistance:
Titanium’s resistance to corrosion ensures longevity, making it suitable for applications in challenging environments.
Lightweight Nature:
Despite its strength, Titanium is remarkably lightweight, reducing overall weight in components without sacrificing structural integrity.
Biocompatibility:
Titanium’s biocompatibility makes it ideal for medical applications, ensuring compatibility with the human body for implants and surgical tools.
High Melting Point:
Titanium’s high melting point enables CNC machining in high-temperature environments, expanding its utility in diverse industrial settings.
Low Thermal Expansion:
The low thermal expansion of Titanium enhances its stability during temperature variations, ensuring precision in CNC machining processes.
Excellent Weldability:
Titanium’s weldability facilitates the seamless integration of components, contributing to the efficiency of CNC machining operations.
Advantages of Aluminum Alloy in CNC Machining
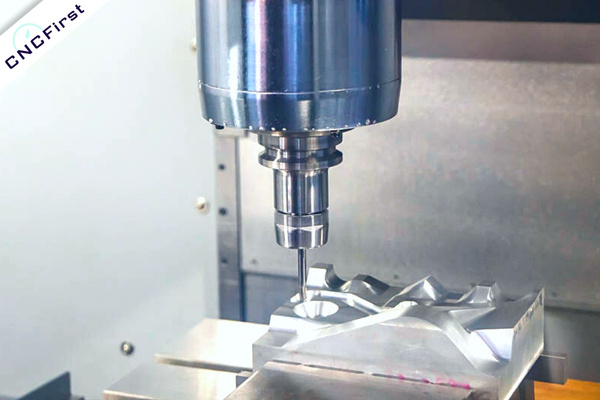
Opting for aluminum in CNC machining unveils a range of advantages, showcasing its versatility and suitability for various applications.
Exceptional Lightweight Nature:
Aluminum’s low density makes it an ideal choice for CNC machining where weight reduction is crucial without compromising structural integrity.
Good Machinability:
Aluminum’s machinability simplifies the CNC machining process, ensuring efficiency and precision in the creation of intricate components.
Thermal Conductivity:
The high thermal conductivity of aluminum alloy facilitates effective heat dissipation, making it suitable for components in electronic devices.
Cost-Effectiveness:
Aluminum’s abundance and ease of extraction contribute to its cost-effectiveness, providing an economical option for CNC machining projects.
Corrosion Resistance:
While not as corrosion-resistant as Titanium, Aluminum can be treated or coated to enhance its resistance, ensuring durability in various environments.
Malleability:
Aluminum’s malleability allows for intricate designs and shapes, offering flexibility in CNC machining for diverse applications.
Comparing the Properties of Titanium vs. aluminum
In the realm of CNC machining, understanding the distinctive properties of materials is crucial. Let’s embark on a detailed exploration of aluminum vs titanium, two metals that stand at the forefront of this precision-driven industry.
Strength and Durability
Mechanical properties play an integral role in engineering metal parts and components.
Titanium: Renowned for its exceptional tensile strength, titanium surpasses aluminum in durability, making it ideal for applications requiring robust components.
Aluminum: While not as strong as titanium, aluminum boasts commendable durability, particularly in scenarios where a lightweight yet resilient material is preferred.
Corrosion Resistance
Titanium: Exhibiting remarkable corrosion resistance, titanium is well-suited for environments where exposure to harsh elements is a concern, ensuring longevity and reliability.
Aluminum: Although susceptible to corrosion, aluminum can be treated or coated to enhance its resistance, making it suitable for various applications.
Weight Considerations
Titanium: Despite its strength, titanium is remarkably lightweight, making it advantageous for applications where minimizing weight is critical without compromising durability.
Aluminum: Known for its low density, aluminum is an exceptionally lightweight material, contributing to its widespread use in industries prioritizing weight efficiency.
Thermal Properties
Titanium: With excellent heat resistance, titanium excels in high-temperature environments, ensuring stability and performance in demanding thermal conditions.
Aluminum: Possessing good thermal conductivity, aluminum efficiently dissipates heat, making it suitable for applications requiring effective thermal management.
Titanium Vs. Aluminum: Comparing Their Applications
In the realm of CNC machining, the choice between titanium and aluminum hinges on their distinct applications, each metal bringing unique attributes to the table.
Titanium Applications:
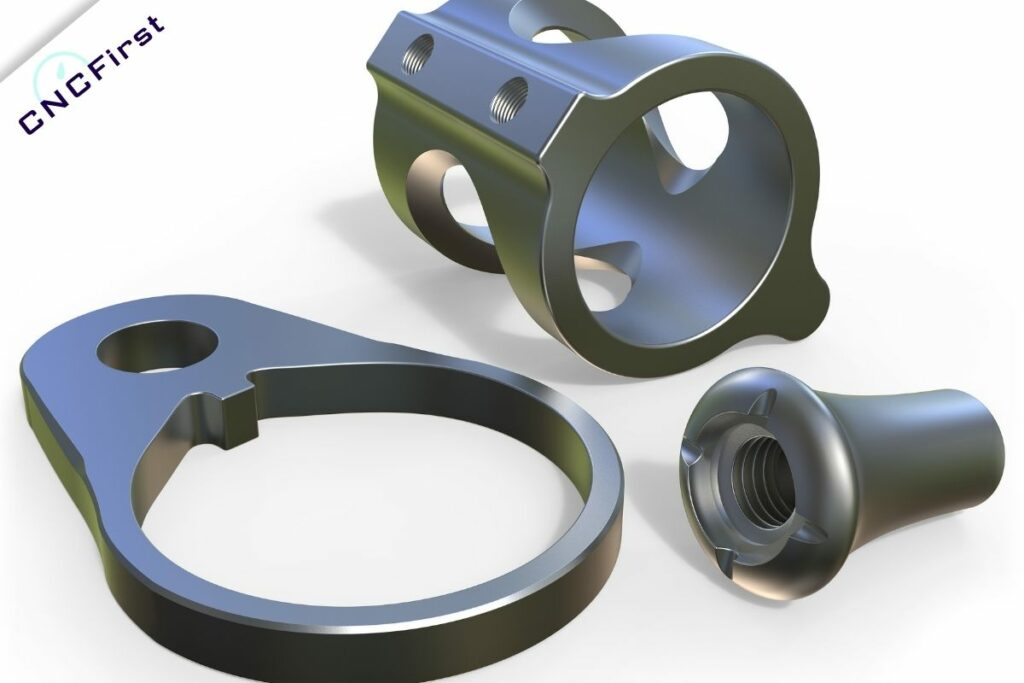
Aerospace Industry:
Titanium’s lightweight yet robust nature makes it a staple in aircraft components, ensuring structural integrity without compromising on weight.
Medical Implants:
Biocompatibility and corrosion resistance position Titanium as a preferred choice for medical implants, providing durability and reduced risk of adverse reactions.
Military Equipment:
Titanium’s strength and resistance to harsh environments make it suitable for military applications, from armor plating to missile components.
Sports Equipment:
The combination of strength and low weight makes titanium desirable for sports gear, enhancing performance in products like golf clubs and bicycle frames.
Marine Engineering:
Titanium’s corrosion resistance finds applications in marine environments, contributing to the durability of ship components and offshore structures.
Aluminum Applications:
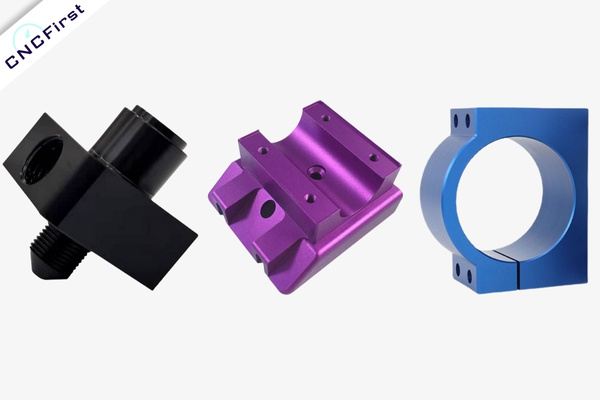
Automotive Industry:
Aluminum’s lightweight composition contributes to fuel efficiency in vehicles, making it a prevalent choice for components like engine blocks and body panels.
Construction Materials:
Aluminum’s corrosion resistance and malleability make it ideal for construction, finding use in window frames, roofing, and structural components.
Packaging Industry:
The malleability and recyclability of aluminum make it a sustainable choice for packaging materials, providing a balance between strength and weight.
Electronics:
Aluminum’s thermal conductivity and lightweight properties find applications in electronic devices, dissipating heat efficiently in products like laptops and smartphones.
Cookware and Utensils:
Aluminum’s heat conductivity makes it a popular choice for cookware, ensuring even heat distribution and quick responsiveness in kitchen applications.
Titanium Vs. Aluminum: Which Lightweight Metal Should You Use?
When choosing between titanium and aluminum for your projects, several factors come into play.
Titanium boasts an exceptional strength-to-weight ratio, making it ideal for applications where lightweight yet robust materials are crucial. Its corrosion resistance and high-temperature tolerance further enhance its suitability in the aerospace and medical industries.
On the other hand, aluminum offers a cost-effective alternative with good strength and corrosion resistance. It is widely used in automotive and construction due to its affordability and malleability.
The decision between titanium and aluminum ultimately depends on your specific needs and budget constraints. Consider the intended application, material properties, and budgetary considerations to make an informed choice for optimal performance and cost-effectiveness
Read more: Titanium Vs. Steel, What Is The Difference?
CNCfirst Manufacturing Capabilities
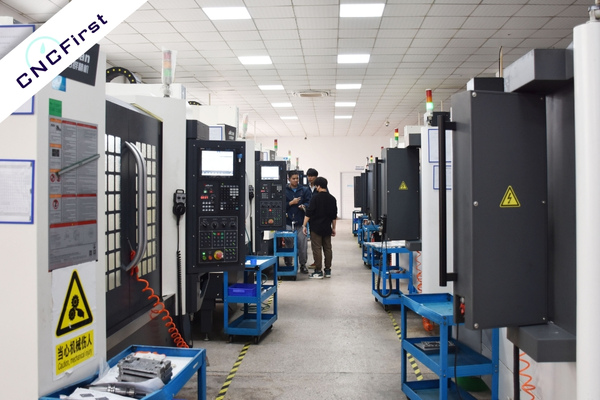
Our state-of-the-art facilities specialize in CNC milling and CNC turning, offering unparalleled precision and efficiency. Whether you require intricate components or large-scale production, our advanced CNC machining processes ensure exceptional accuracy and quality. Additionally, we excel in rapid prototyping, providing a swift and cost-effective solution for product development and testing.
At CNCfirst, we are committed to delivering top-notch manufacturing services tailored to your specifications. Contact us to harness the expertise of our skilled team and leverage the capabilities of CNC milling, CNC turning, and rapid prototyping for your projects. Take your manufacturing endeavors to new heights with CNCfirst’s dedication to excellence and innovation.
Conclusion
In the intricate world of CNC machining, the choice between Titanium and Aluminum is a nuanced decision, each metal bringing unique advantages to the table. Whether prioritizing Titanium’s strength and biocompatibility or opting for Aluminum’s lightweight design and cost-effectiveness, precision engineering projects find tailored solutions. The applications, elemental compositions, and advantages of these metals underscore the importance of informed decision-making.
Ultimately, the optimal choice depends on project requirements, industry demands, and the delicate balance between strength, weight, and cost. As CNC machining continues to evolve, embracing the versatility of Titanium and Aluminum ensures a future of precision and innovation.
FAQs
Is Titanium better than Aluminum for CNC machining?
Titanium excels in strength and durability, making it suitable for robust applications. However, the choice depends on specific project requirements, with Aluminum offering advantages in terms of lightweight design.
What are the cost differences between aluminum and titanium in CNC machining?
Titanium tends to be more expensive than aluminum due to its extraction and processing complexities. Aluminum is a cost-effective alternative, making it suitable for budget-conscious projects.
Can Aluminum replace Titanium in specific applications?
While aluminum may not match titanium’s strength, it can replace it in applications prioritizing lightweight design and cost efficiency. Assess the project’s demands to determine the suitability of Aluminum as a replacement.
How does the choice between Titanium and Aluminum impact CNC machining precision?
The choice influences precision differently; Titanium offers robustness, and aluminum provides efficient machinability. The decision should align with project requirements, ensuring the desired level of precision in CNC machining operations.