You are eager to learn more about CNC machining but don’t know where to start. This beginner’s guide will teach you what you need to know about this essential manufacturing process. We’ll walk you through the basics of CNC machining, from its operations to its machine types.
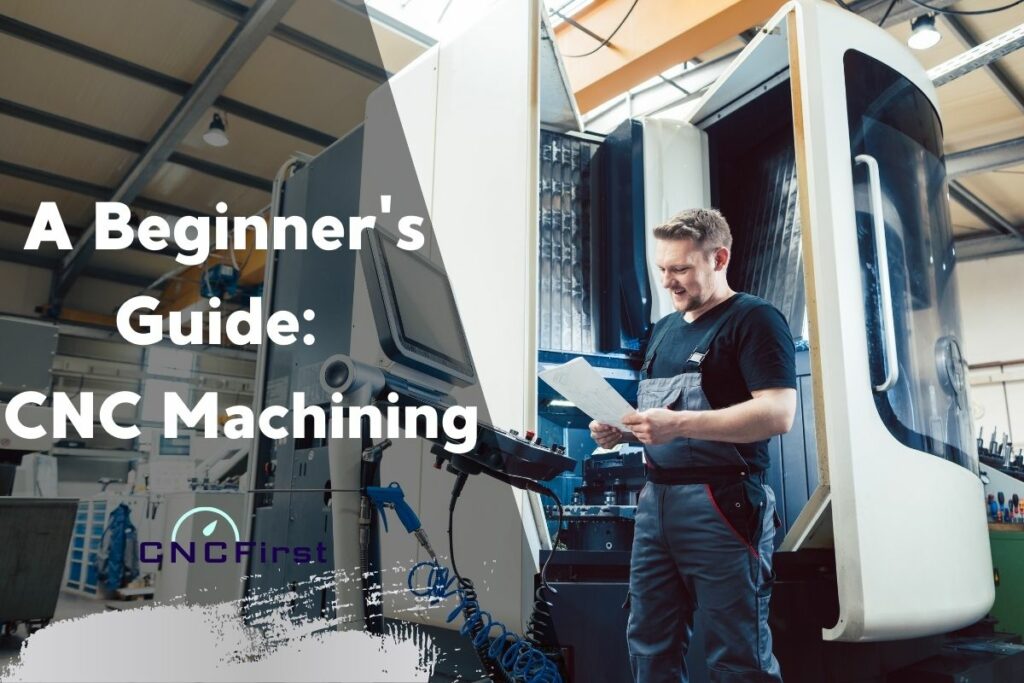
CNC Machining: Definition
CNC machining is a manufacturing process that computer numerically controlled machine tools are used to remove material from a workpiece to create the shape.
The process can be used to create small and large parts and is widely used in various industries, including aerospace, automotive, and medical.
CNC machining is a versatile manufacturing process used to create parts with complex shapes. The process is also relatively fast and accurate, making it well-suited for large production runs.
CNC machining can be performed on various materials, including metals, plastics, and composites.
What’s The CNC Machining Process
The process can be used to create both prototypes and production parts, and is typically used for high-precision work. These parts can be made from metals, plastics, or composites.
The CNC machining process can be used to create a wide variety of shapes and sizes, and can be used to create both functional and decorative parts.
The basic CNC machining process includes the following stages:
- Design of the CAD (Computer-Aided Manufacturing) model
- Convert the CAD files to a CNC program
- Prepare CNC machine tools
- Execute processing operations
CNC Machining: Different CNC Machining Operations
There are numerous CNC machining operations can be performed, including CNC turning, milling, and drilling. Each operation uses specific tools and techniques to create a workpiece’s desired shape or finish.
CNC Turning
CNC turning is a machining process where parts are produced by removing material from a cylindrical workpiece using CNC-controlled lathes. It is a cost-effective alternative to traditional methods such as manual machining.
CNC Milling
CNC milling uses computerized controls to operate milling machines. The mills are equipped with rotary cutting tools that can rapidly remove material from workpieces to produce the desired shape.
And CNC milling produces small and intricate parts, such as those used in the medical and aerospace industries.It can also create larger parts, such as engine blocks and structural components.
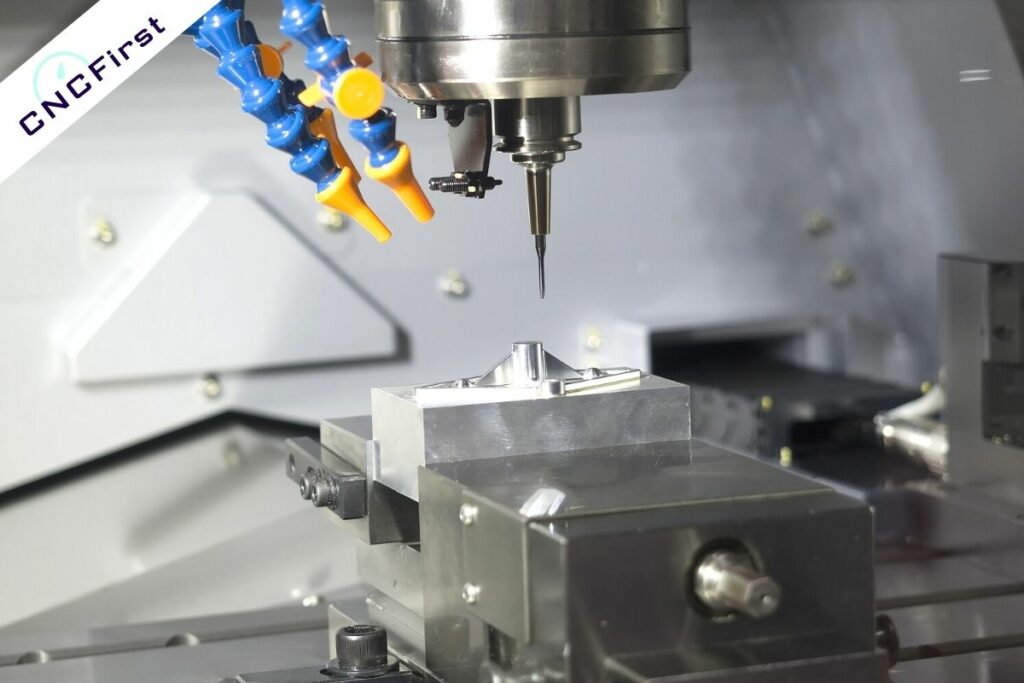
CNC Drilling
CNC drilling is a process of drilling holes into a workpiece. This type of drilling is often used for industrial applications, as it can be more precise and faster than traditional methods.
CNC drilling machines can be programmed to create various hole sizes and patterns, making them versatile for different projects.
Related Machining Articles: CNC Milling: Its Definition, Machines, And Operations CNC Turning: Its Definition, Machines, And Operations
CNC Machining: Different Types Of CNC Machines
The machining is a versatile and precise manufacturing process, and numerous automate machines are designed for CNC machining.
CNC Milling Machine
Mill Machine is a computer numerical controlled machine which means it is operated with the help of a computer. It is mainly used for machining various materials using various machine tools. It includes 3-axis, 4-axis, and 5-axis CNC machine.
Mills consist of three main parts: the controller, spindle, and axes. The controller is responsible for receiving the input from the computer and translating it into commands for the machine. The spindle is the machine part that holds and rotates the cutting tool. Axes are the parts of the machine which move the cutting tool in different directions.
CNC Milling Machines can be operated manually or automatically. When operated manually, the operator inputs the commands into the computer, and when operated automatically, the computer controls the machine according to pre-programmed instructions.
CNC Lathe Machine
CNC lathes are computer-controlled lathe machines that turn cylindrical rods at very precise speeds. The speed and stopping points of the rod are all set by a computer program, which the operator inputs before beginning the machining process.
CNC lathes use a cutting tool that is mounted on a movable carriage. The carriage is controlled by a computer, which allows for much greater precision and repeatability than what is possible with manual operations.
CNC Drilling Machine
The CNC Drilling Machine consists of three main parts: the spindle, the table, and the CNC controller.
The spindle is the part of the machine that drills the holes. It is driven by a motor and can spin at high speeds. The table is where the workpiece is placed. The CNC controller is what controls the spindle and table. It is programmed with a CNC program that tells it how fast to spin the spindle and how to move the table.
The CNC controller is what makes a CNC Drilling Machine work. Without it, the machine would be nothing more than a regular drilling machine.
CNC Laser Cutting Machine
CNC Laser Cutting Machine is a computer-controlled cutting machine that cuts materials like wood, paper, metal, etc.
It uses a laser beam to cut the material. The cutting machine is controlled by a computer that contains a set of instructions or a CNC program.
The program tells the machine what material to use, how thick the material is, the workpiece’s size and shape, and the cutting beam’s speed and direction.
Laser Cutting Machines are classified according to their power source: CO2, fiber, or carbon dioxide lasers are the three most common types.
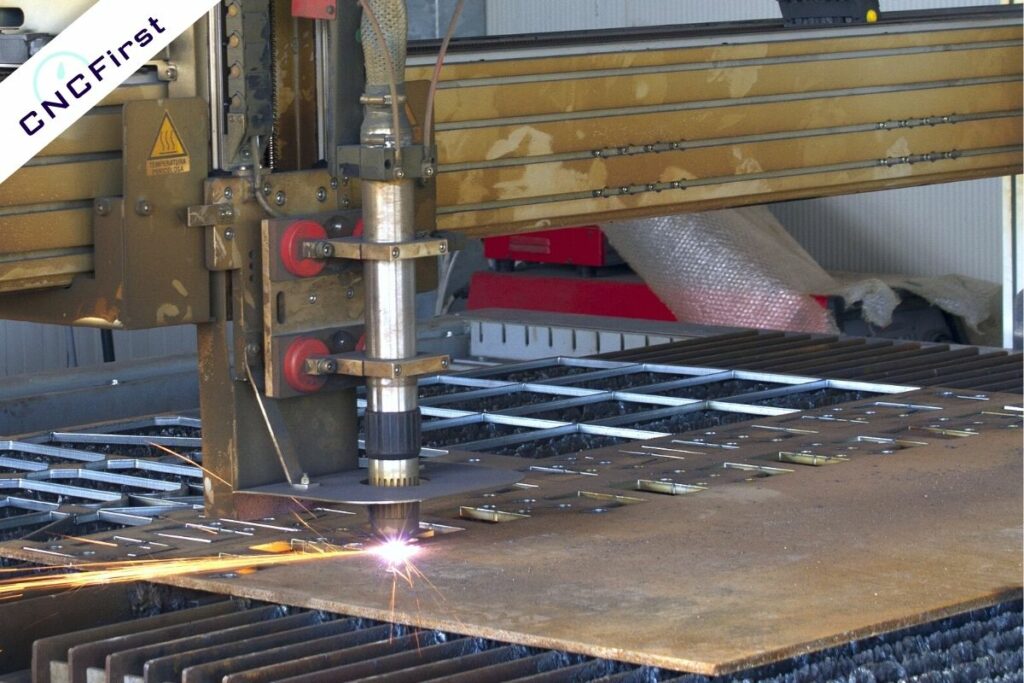
CNC Waterjet Cutting Machine
CNC Waterjet Cutting Machine is a kind of CNC machine which uses high-pressure water to cut metals.
It works by using a high-pressure pump to increase the water pressure to more than 60,000 psi. Then the water is focused through a narrow nozzle, creating a very high-velocity jet. When this jet comes into contact with the metal, it can cut through it.
CNC Plasma Cutting Machine
CNC Plasma Cutting Machine uses a plasma torch to cut through the metal.
The torch is connected to an electrode connected to a CNC controller. The CNC controller tells the torch where and how deep to cut. Plasma cutting is a very accurate way to cut metal and can be used to create intricate designs.
Plasma Cutting Machines are used in various industries, including aerospace, automotive, and architecture.
CNC Electrical Discharge Machine
CNC Electrical Discharge Machines work by using electrical current to erode the metal. A dielectric fluid is used to carry the electrical current between the workpiece and the electrode. The fluid also helps to cool the workpiece and electrode, preventing them from overheating.
Electrical discharge machining is commonly used to create cavities and other complex shapes in metal parts.
CNC Router Machine
CNC Router Machine is a computer-controlled machine that cuts and routes out different materials. They are often used in woodworking but can also be used on other materials, including aluminum, plastics, and glass.
CNC routers are very precise and can create very intricate designs. The machine itself consists of a router bit attached to a moving spindle. The spindle is controlled by a computer program that tells it how fast to spin and in what direction to move. The router bit is then guided along the cut material, following the specific design that has been programmed into the computer.
CNC Machining: Procedures
The CNC machining process creates a computer-aided design (CAD) file at the beginning. This file contains the detailed dimensions and tolerances of the desired part. The CAD file is then downloaded to a CNC machine, programmed to follow the instructions in the file.
Once the CNC machine is programmed, the operator initiates the machining cycle. The machine will then move the cutting tool through the workpiece, removing material and creating the desired shape.
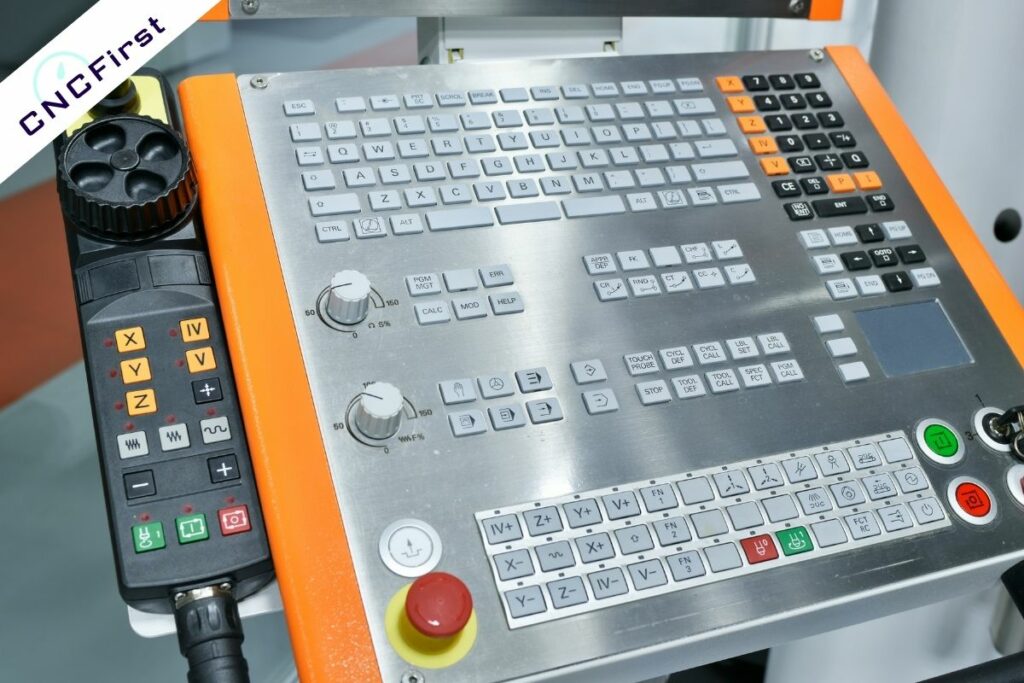
What’s the Difference Between CNC Machining And 3D Printing?
Process: CNC (Computer Numerical Control) machining involves subtractive manufacturing, where material is removed from a solid block to create the desired shape, while 3D printing, also known as additive manufacturing, builds objects layer by layer from digital designs.
Material Compatibility: CNC machining can work with a wide range of materials including metals, plastics, and composites, offering more material versatility compared to 3D printing which is often limited to specific types of plastics, resins, metals, and some composites.
Accuracy: CNC machining typically offers higher precision and surface finish quality, making it suitable for applications requiring tight tolerances, while 3D printing may have limitations in accuracy and surface finish depending on the technology and settings used.
Complexity: 3D printing excels in producing complex geometries and intricate designs with minimal post-processing, whereas CNC machining may struggle with intricate internal features or overhangs without additional support structures or post-processing.
Speed: CNC machining is generally faster for producing larger quantities of parts, while 3D printing can be more time-consuming, especially for complex designs or large objects, due to its layer-by-layer approach.
FAQs:
Q: What Is CNC?
CNC represents computer numerical control. The basis of CNC is NC (numerical control), which appeared in the 1940s. With the automate progress of computer hardware and software technology, CNC gradually evolved from NC. Compared with traditional manual processing, CNC technology has the advantages of high precision, repeatability, efficiency, and economy. This method can replace additive manufacturing processes, such as 3D printing.
What is the history of CNC machining?
This technology has been around since the 1950s, when it was first used for manufacturing aircraft components. Today, CNC machining is used in a variety of industries, from automotive to aerospace. The history of CNC machining can be traced back to the early days of computing.
Q: Who invented CNC Machining?
The first CNC machine was invented in the 1950s by John T. Parsons, who developed the technology while working on missile guidance systems for the US military. Since then, CNC machines have become an essential part of modern manufacturing, with usage ranging from small home hobbyists to large industrial manufacturers.
Q: Which material to choose for CNC machining?
There are many different materials that can be machined using CNC technology, including metals, plastics, and composites.
Materials: aluminum, copper, brass, stainless steel, and titanium
Plastics: acrylic, nylon, PEEK, POM, ABS, and more.
Each material has its own unique properties that must be considered when choosing which material to use for a particular application.
Some factors that should be considered when choosing a material for CNC machining.
It includes the hardness of the material, the strength of the material, the weight of the material, and the cost of the material.
In general, harder materials are more difficult to machine but can withstand higher levels of stress and wear.
Q: What are the Advantages of CNC Machining?
There are many advantages of CNC machining, including:
1. Increased Productivity: CNC machines can work 24 hours a day, 7 days a week without tiring, which increases productivity and output.
2. Greater Accuracy: With CNC machining, there is little room for error as the machine carries out the precise instructions provided by the CAM program.
3. Increased Flexibility: CNC technology gives manufacturers the flexibility to quickly produce small batches or prototypes of new products without incurring high tooling costs.
Conclusion
CNC machining can be a great way to create precision parts for your project. Hopefully, this guide has given you a better understanding of CNC Machining.
There are many CNC machining manufacturers in China. We are a professional China manufacturer, and provide custom machining services. If you need help deciding which process will work best for your project or want some advice on what type of part would suit your application, please visit our homepage and contact us today. We are glad to discuss your project with you and provide you with a free quote.