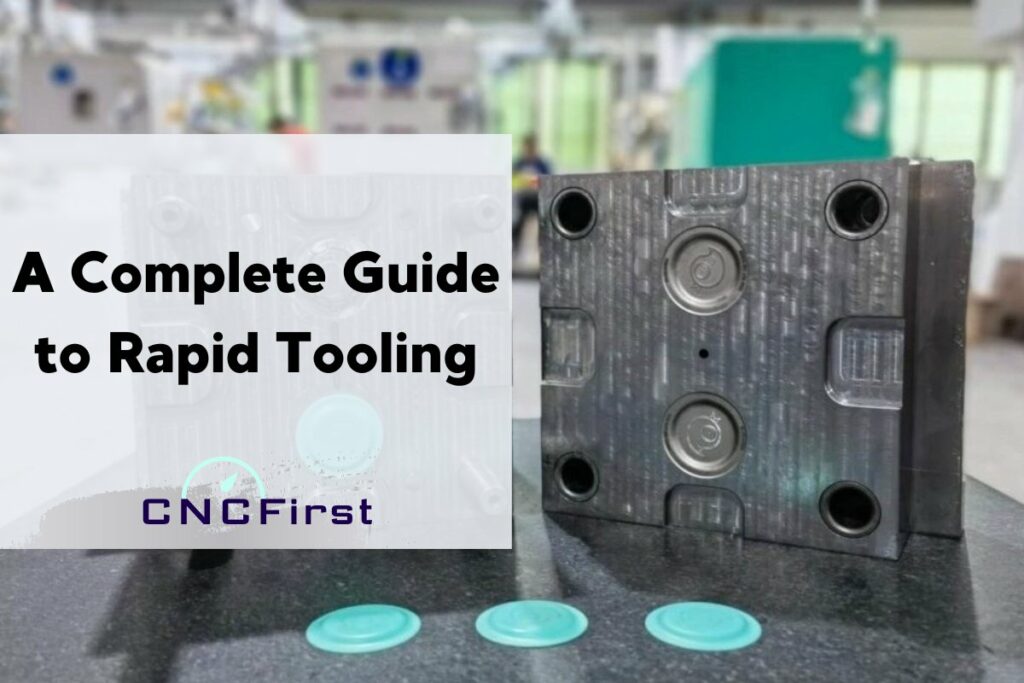
In today’s fast-paced manufacturing landscape, companies are constantly seeking ways to reduce time-to-market and optimize their product development processes. One such technique that has gained significant popularity is rapid tooling. This article aims to provide a complete guide to rapid tooling, covering its definition, various techniques, benefits, limitations, case studies, and the future of this innovative manufacturing approach.
What is Rapid Tooling?
Rapid tooling is a manufacturing process that enables the rapid production of tooling components, such as molds, dies, and fixtures, to expedite the production of end-use parts. It involves the utilization of advanced techniques and technologies to create these tools in a shorter time frame compared to traditional tooling methods.
Importance of Rapid Tooling
Rapid tooling plays a vital role in accelerating product development cycles and reducing time-to-market. By enabling faster production of tooling components, companies can bring their products to market more quickly, gaining a competitive edge. Moreover, it facilitates design iterations and modifications, allowing for faster design validation and optimization.
Types of Rapid Tooling
There are three main types of rapid tooling: prototype tooling, bridge tooling, and production tooling. Each type serves a specific purpose in the product development process.
Prototype Tooling
Prototype tooling involves the creation of tooling components for the production of functional prototypes. It allows manufacturers to test and evaluate the design, fit, and functionality of a part before moving to mass production.
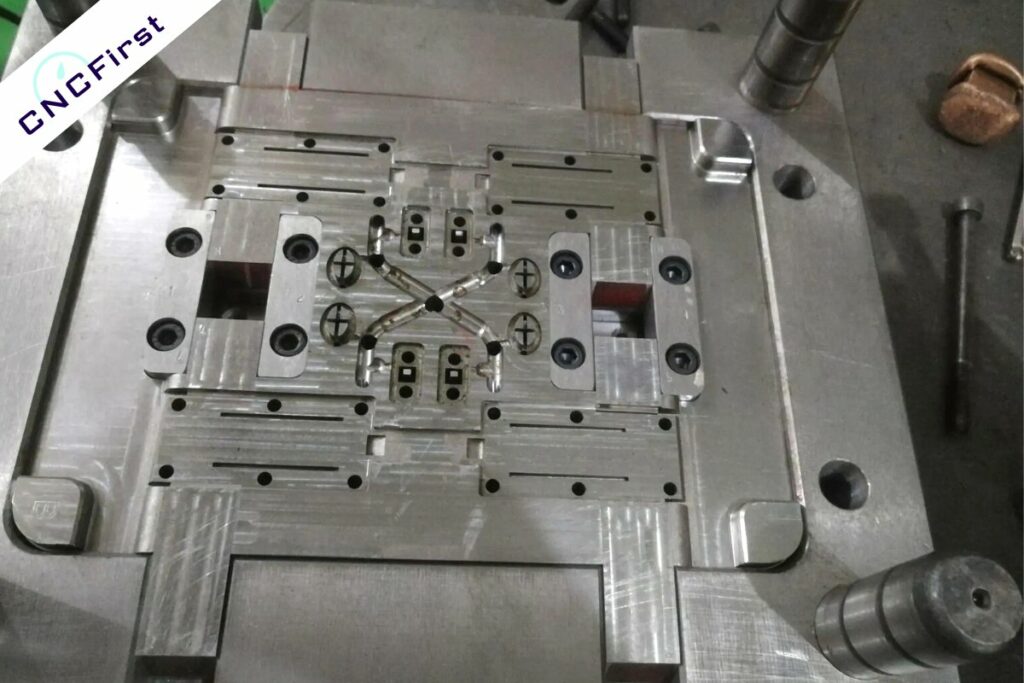
Bridge Tooling
Bridge tooling fills the gap between prototype tooling and full-scale production tooling. It is used when a small production run is required to bridge the transition from prototyping to mass production. Bridge tooling enables manufacturers to validate the design, test the manufacturing process, and produce a limited quantity of parts for market testing or early customer feedback.
Production Tooling
Production tooling is the final stage, where the tooling components are manufactured for large-scale production. It involves creating durable and long-lasting molds, dies, or fixtures that can withstand the demands of high-volume manufacturing.
Benefits of Rapid Tooling in Injection Molding
The adoption of rapid tooling in injection molding offers several benefits for manufacturers aiming to streamline their product development processes.
Faster Time to Market
Rapid tooling significantly reduces the time required for tooling production, resulting in faster time-to-market for new products. With reduced lead times, manufacturers can respond to market demands quickly and gain a competitive advantage.
Cost Reduction
Traditional tooling methods often involve substantial costs associated with tooling design, machining, and modification. Rapid tooling eliminates some of these expenses by utilizing cost-effective technologies such as additive manufacturing or CNC machining. It also minimizes the costs associated with design changes during the development process.
Design Validation
Manufacturers can validate and test the design of their plastic parts before committing to mass production. By producing functional prototypes or low-volume parts, design flaws and issues can be identified and resolved early on, leading to improved product quality and performance.
Rapid Tooling Techniques
Several techniques are employed in rapid tooling, depending on the specific requirements of the project. The most commonly used techniques include additive manufacturing, CNC machining, and vacuum casting.
Additive Manufacturing
Additive manufacturing, also known as 3D printing, is a versatile technique. It involves the layer-by-layer deposition of material to create tooling components. Additive manufacturing offers design freedom, allowing the production of complex geometries that are difficult to achieve through traditional machining methods.
CNC Machining
CNC machining is a subtractive manufacturing process that utilizes computer-controlled machines to shape tooling components from solid blocks of material. It provides high precision and accuracy, making it suitable for producing tooling components with tight tolerances.
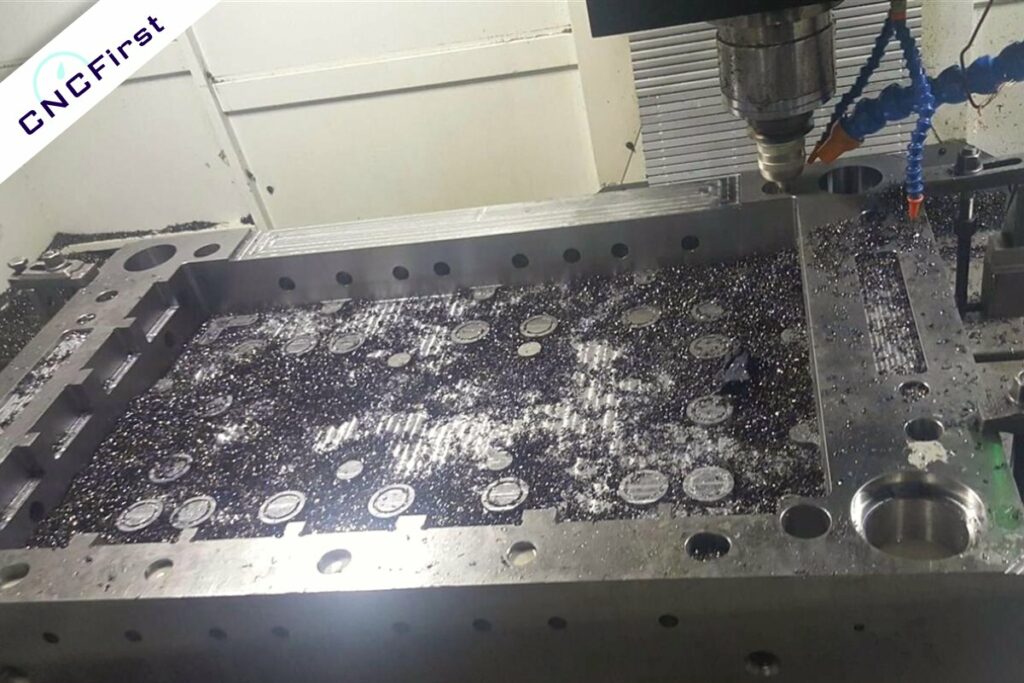
Vacuum Casting
Vacuum casting creates silicone molds from a master pattern. It enables the production of multiple copies of a part using various materials. Vacuum casting is particularly useful when a small batch of parts is required for testing or market evaluation.
Rapid Tooling Vs Rapid Prototyping
Rapid tooling and rapid prototyping are two distinct but interconnected processes in the realm of product development.
The rapid prototyping process focuses on quickly creating physical models or prototypes of a product to test its design, fit, and functionality.
It utilizes techniques like 3D printing or CNC machining to rapidly produce prototypes directly from digital designs.
On the other hand, rapid tooling involves the rapid production of molding components, such as molds or dies, to expedite the manufacturing of end-use parts.
It enables the creation of functional prototypes or low-volume production runs using cost-effective tooling methods like additive manufacturing or vacuum casting.
While rapid prototyping primarily aims to validate the design, rapid tooling extends the capabilities by providing functional parts for testing and evaluation.
Both processes complement each other in accelerating product development and reducing time-to-market, offering manufacturers efficient ways to iterate designs and optimize their products.
Factors to Consider When Making Prototype Molds
When opting for prototyping molds, several factors need to be considered to ensure the success of the project.
Material Selection
Choosing the right material for tooling components is crucial. Factors such as part requirements, expected lifespan, and production volume should be taken into account when selecting materials. Common materials include various grades of steel, aluminum, and high-performance plastics.
Part Complexity
The complexity of the part needs to be considered. Some techniques may be better suited for producing parts with intricate geometries or fine details, while others are more suitable for simpler designs.
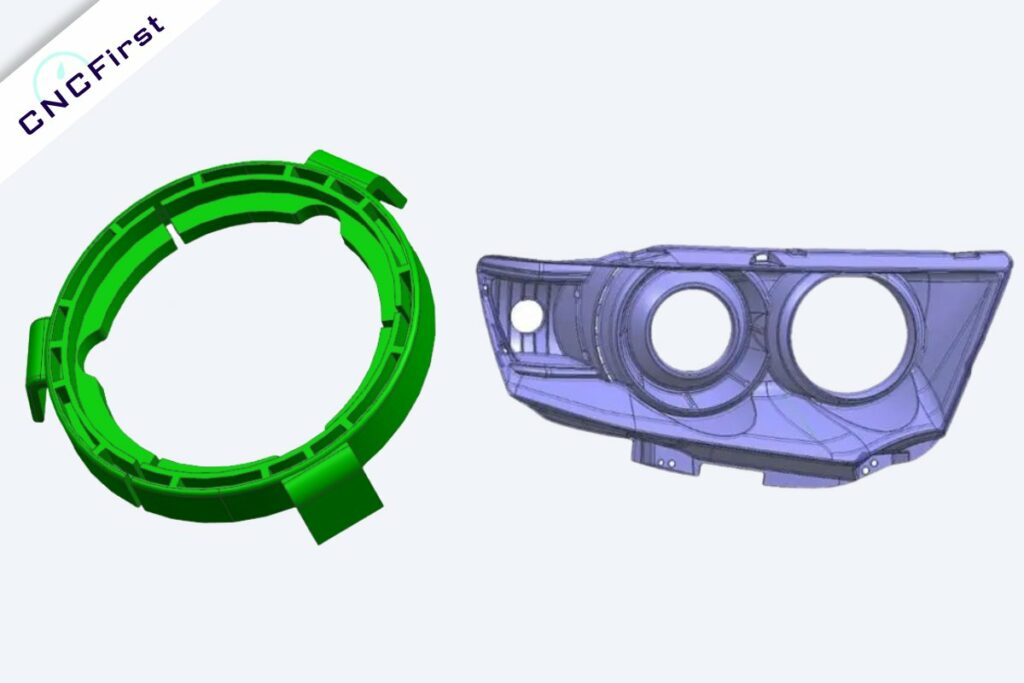
Volume Requirements
You also need to consider the production volume. Some techniques, such as 3D printing, are more cost-effective for low-volume production, while others, like CNC machining, can handle larger production runs.
Limitations and Challenges of Rapid Tooling
While rapid tooling offers numerous advantages, it is essential to be aware of its limitations and challenges.
Accuracy and Tolerance
Achieving tight tolerances and high accuracy can be challenging with rapid tooling techniques. The dimensional accuracy of tooling components may vary depending on the chosen technique and material. Careful consideration is required when selecting it for applications with strict dimensional requirements.
Limited Material Choices
Compared to traditional tooling methods, rapid tooling may have limited material options. Some materials used in traditional toolings, such as hardened steel, may not be suitable for rapid tooling due to the limitations of the chosen technique. However, advancements in materials are continually expanding the available options.
Production Volume Limitations
While rapid tooling techniques can handle low to medium production volumes effectively, they may not be as cost-efficient or suitable for large-scale production. Manufacturers should assess their production volume requirements and select the appropriate tooling method accordingly.
Industry Applications
To illustrate the real-world application and benefits of rapid tooling, let’s explore two case studies from different industries.
Automotive Industry
In the automotive industry, rapid tooling has revolutionized the product development process. Manufacturers can quickly produce functional prototypes for design validation and testing, significantly reducing the time required for new vehicle development.
Consumer Electronics Industry
The consumer electronics industry relies on rapid tooling to keep up with the fast-paced market demands. By using these techniques, manufacturers can rapidly prototype and produce high-quality casings, connectors, and other components. This allows for faster product iterations, ensuring that consumer electronics devices stay ahead in terms of design, functionality, and aesthetics.
Choose Our Rapid Tooling Services For Injection Molding
At our company, we pride ourselves on our machining tooling capabilities for injection molding. We understand that time is of the essence when it comes to getting your products to market, so we work quickly and efficiently to get your tools made as fast as possible.
And we own the latest technology and equipment to produce high-quality molds that will meet your exact specifications. We can handle your project efficiently whether you need a hundred or some thousand units or thousand.
Molds are always relatively expensive; using rapid prototyping techniques such as 3D printing, which our company handed, can drastically reduce their cost. Contact us today to learn more about rapid prototyping services!
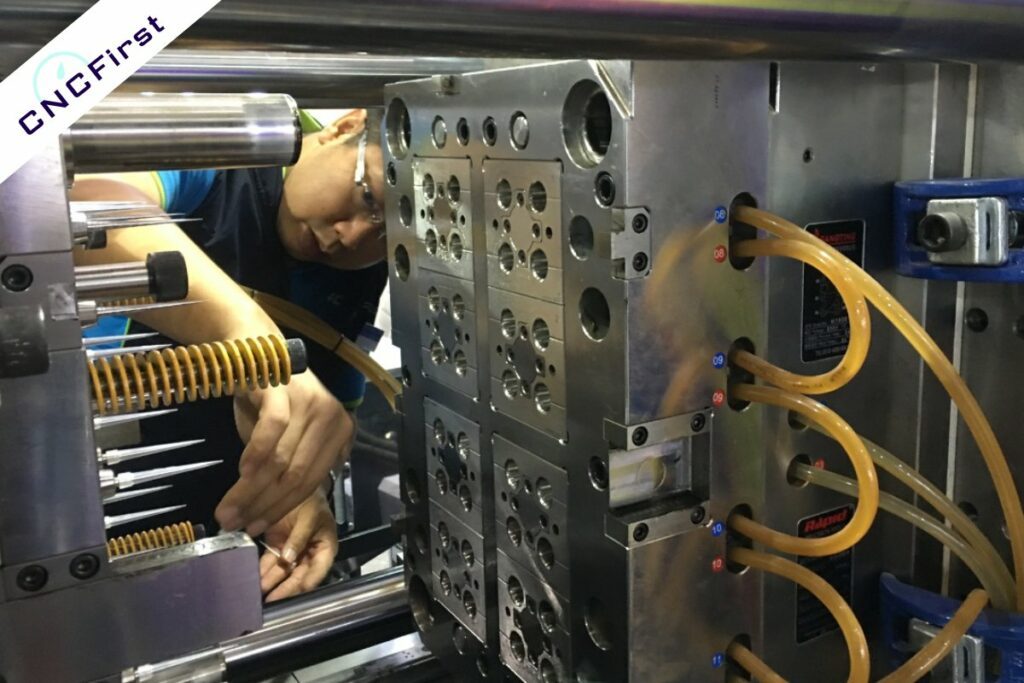
Conclusion
Rapid tooling is a game-changing manufacturing approach that offers numerous benefits for companies looking to streamline their product development processes. By reducing time-to-market, cutting costs, and enabling design validation, manufacturers can stay competitive in today’s dynamic business landscape.
FAQs
Q: How Does Rapid Tooling Differ From Traditional Tooling?
Rapid tooling differs from traditional tooling in terms of speed and cost-effectiveness. It utilizes advanced technologies like additive manufacturing and CNC machining, allowing for faster production of tooling components at a reduced cost compared to conventional tooling methods.
Q: Can Rapid Tooling Be Used For High-Volume Production?
While rapid tooling techniques are suitable for low to medium production volumes, they may not be as cost-efficient or suitable for large-scale production. The selection of methods should consider the specific production volume requirements.
Q: How Does Rapid Tooling Contribute To Design Optimization?
Rapid tooling allows for faster design iterations and modifications, enabling manufacturers to optimize their product designs before committing to mass production. By producing functional prototypes, design flaws, and issues can be identified and resolved early on, leading to improved product performance and customer satisfaction.
Q: What Are The Cost Implications Of Rapid Tooling?
It can offer cost savings compared to traditional methods. By reducing lead times and eliminating some of the costs associated with design changes and modifications, manufacturers can achieve significant cost reductions throughout the product development process.
Q: Soft Tooling Vs. Hard Tooling In Injection Molding, What’s Different?
In injection molding, soft tooling, and hard tooling are two commonly used approaches for creating molds.
Soft tooling, also known as prototype tooling or bridge tooling, involves the use of less durable materials such as aluminum or epoxy to create molds.
Soft tooling is typically used for low-volume production runs or prototyping purposes. It offers faster turnaround times and lower costs compared to hard tooling.
However, soft tooling has limitations in terms of durability and longevity, making it less suitable for high-volume production.
In contrast, hard tooling utilizes hardened steel to create mold parts that can withstand the demands of high-volume manufacturing.
Hard tooling provides excellent precision, repeatability, and durability, making it ideal for large-scale production.
While hard tooling requires higher initial investment and long lead times, it offers long-term cost savings and superior performance.
The choice between soft tooling and hard tooling depends on factors such as production volume, project timeline, and budgetary considerations.