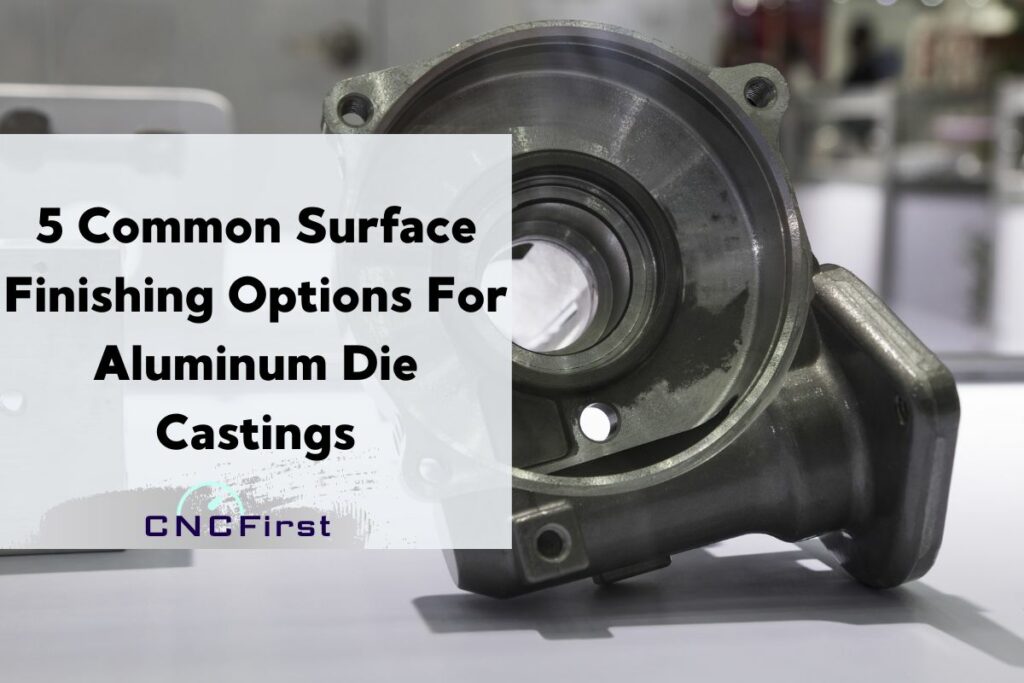
In the realm of manufacturing, aluminum die casting stands out as a widely employed technique, ensuring the production of intricate and durable components. However, the journey doesn’t conclude with casting; the surface finishing for aluminum die castings emerges as a critical phase.
This article delves into the nuances of this crucial process, exploring its significance in enhancing not only the aesthetics but also the functionality and longevity of aluminum die-cast products. Join us on an exploration of the pivotal role that surface finishing plays in elevating the quality and performance of aluminum die castings.
Importance of Surface Finishing for Aluminum Die Cast Parts
Surface finishing for aluminum or zinc die castings holds paramount importance, contributing to various facets that significantly impact the overall quality and performance of the products.
A. Enhancing Aesthetics and Visual Appeal
Surface finishing serves as the artistic touch, transforming raw aluminum die castings into visually appealing products. Techniques such as anodizing and powder coating not only add vibrant colors but also create a polished and sophisticated appearance, meeting the aesthetic expectations of consumers.
B. Improving Corrosion Resistance
One of the primary challenges faced by aluminum components is susceptibility to corrosion. Through strategic surface finishing, a protective layer is added, acting as a robust barrier against corrosive elements. This not only preserves the structural integrity but also prolongs the lifespan of the die-cast products.
C. Enhancing Wear Resistance
Die-cast components often encounter wear and tear in their operational life. Surface finishing methods, such as chromate conversion coating, are adept at fortifying aluminum against abrasion, ensuring that the products endure challenging environments without compromising their functionality.
D. Meeting Functional Requirements
Beyond aesthetics, surface finishing is tailored to meet specific functional demands. Whether it’s enhancing conductivity through anodizing or ensuring a non-slip surface for better grip, the choice of finishing technique directly aligns with the intended purpose and application of the die-cast aluminum products.
In essence, surface finishing plays a multifaceted role, elevating the overall quality, durability, and functionality of aluminum die castings.
Common Surface Finishing for Aluminum Die Castings
When it comes to enhancing the surface of aluminum die cast parts, several techniques take center stage, each offering unique advantages and considerations. Let’s delve into the prominent methods that define the landscape of surface finishing for aluminum die castings.
Anodizing
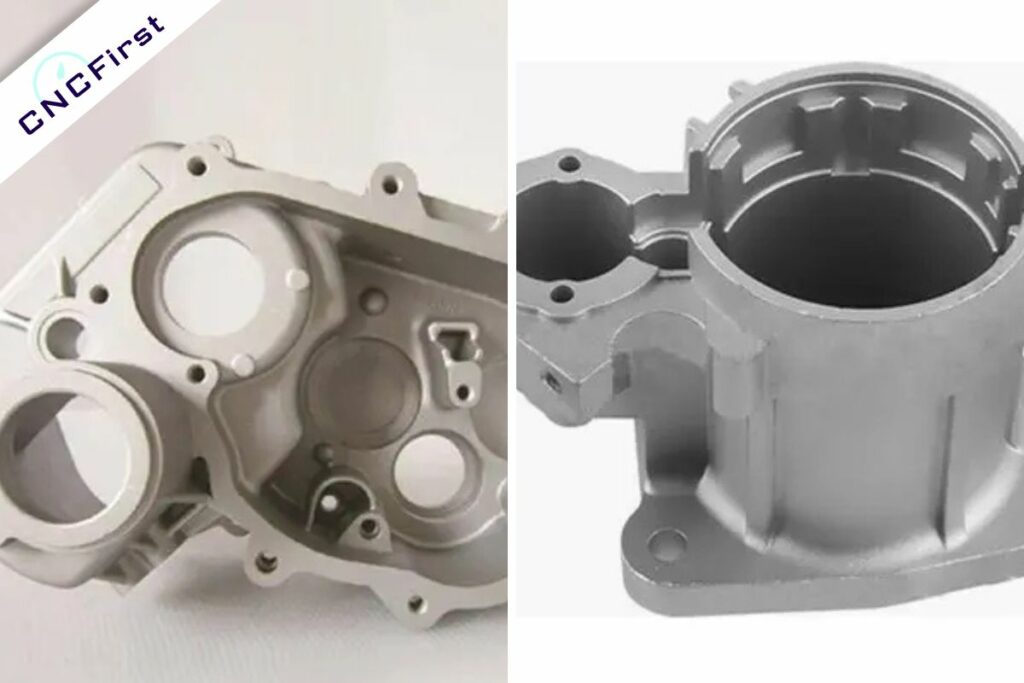
Process Overview: Anodizing involves the electrochemical conversion of the aluminum surface into a durable, corrosion-resistant oxide layer. This process not only adds a protective coating but also enhances the aesthetic appeal of the die-cast components.
Benefits for Aluminum Die Castings: Anodizing bestows a range of benefits, including increased corrosion resistance, improved hardness, and the ability to retain vibrant colors. It is a preferred choice for applications where both durability and visual appeal are crucial.
Considerations and Limitations: While anodizing offers commendable protection, it may alter the dimensions of the die-cast parts. Additionally, achieving uniform color can be challenging, requiring meticulous control over the process parameters.
Powder Coating
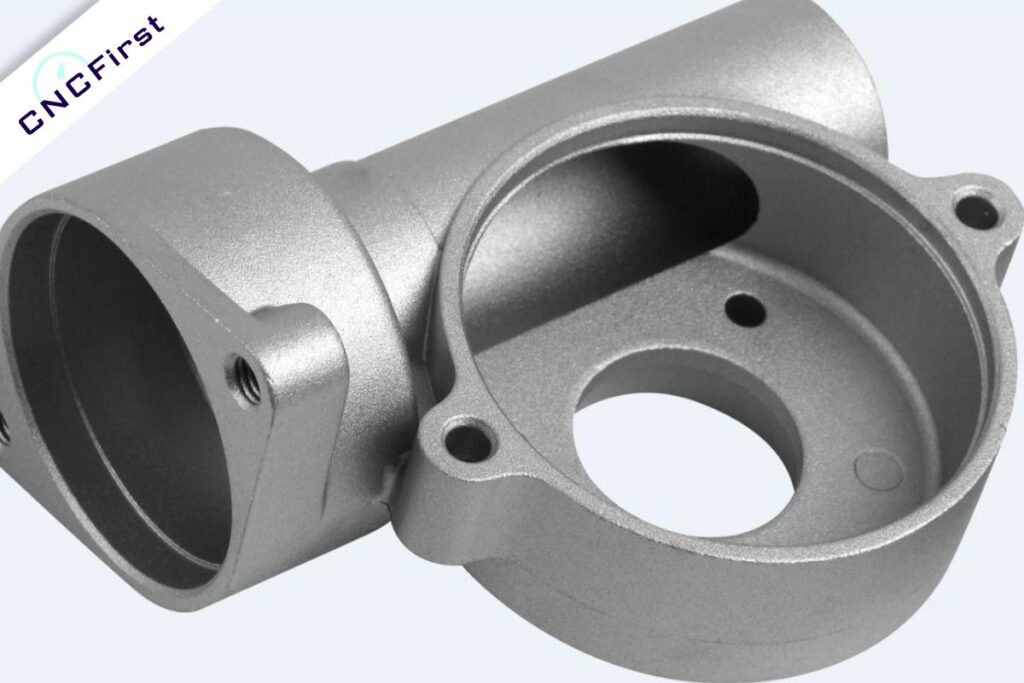
Application Process: Powder coating involves the electrostatic application of dry powder onto the die-cast surface, followed by curing to create a durable and protective finish. This method ensures an even coating and is well-suited for complex shapes and large volumes.
Advantages in Die Casting: The versatility of powder coating allows for a wide range of colors and finishes, providing not only protection against corrosion but also an attractive and smooth surface. It is a cost-effective solution for large-scale production.
Key Considerations: While powder coating is durable, it may be susceptible to chipping in high-impact situations. Proper surface preparation and coating thickness are critical factors to ensure optimal performance.
Chromate Conversion Coating
Purpose and Benefits: Chromate conversion coating involves the application of a chromate solution to form a protective layer on the die-cast surface. This method enhances corrosion resistance and serves as a primer for subsequent coatings.
Application in Die Castings: Widely used in aerospace and automotive industries, chromate conversion coating provides an excellent base for paints and other finishes. It offers a balance between protection and maintaining the original surface appearance.
Environmental Considerations: While effective, chromate conversion coatings raise environmental concerns due to the use of hexavalent chromium. Innovations in eco-friendly alternatives are being explored to address these environmental considerations.
Electrophoretic Painting
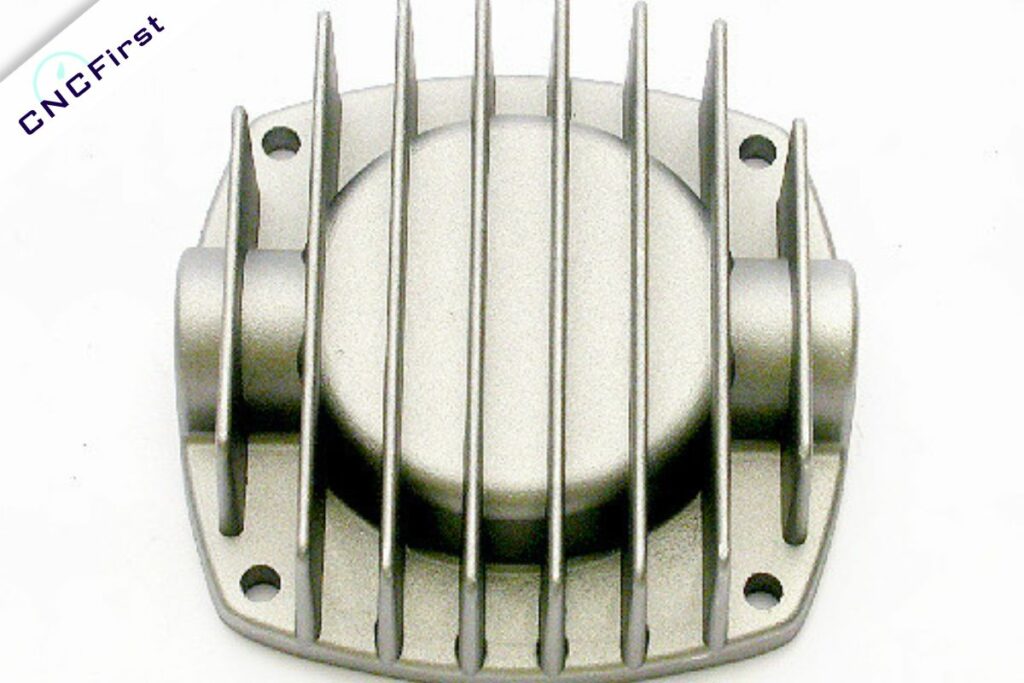
Process Explanation: Electroplate, or e-coating, involves immersing the die-cast components in a bath of paint, and an electric current is used to deposit the paint evenly across the surface. This process ensures a uniform and durable coating.
Advantages and Challenges: Electrophoretic painting provides excellent coverage, corrosion resistance, and even distribution of the coating. However, challenges may arise in coating recessed areas, requiring careful process optimization.
Applicability in Aluminum Die Castings: Particularly effective for complex geometries and intricate parts, electrophoretic painting is gaining popularity in the aluminum die-casting industry for its ability to achieve consistent and high-quality finishes.
Polishing
Process: Polishing, a meticulous mechanical process, involves the abrasion of the die-cast aluminum surface to achieve a smooth, reflective finish. This method utilizes polishing compounds and abrasive materials to remove imperfections and create a lustrous appearance.
Advantages: Polishing enhances the aesthetic appeal of aluminum die castings by creating a mirror-like finish. Beyond aesthetics, it improves corrosion resistance and facilitates easier cleaning, making polished surfaces both visually appealing and functionally superior in various applications.
Factors Influencing Surface Finish Selection
Selecting the appropriate surface finish for aluminum die castings is a nuanced process, influenced by a combination of factors that range from material characteristics to regulatory compliance.
A. Material Characteristics
The intrinsic properties of the aluminum alloy used play a pivotal role in determining the suitable surface finish. Factors such as alloy composition, hardness, and thermal conductivity impact the compatibility and effectiveness of various finishing techniques.
B. End-Use Applications
The intended application of the die-cast components is a crucial factor in surface finish selection. Considerations revolve around the environmental conditions, functional requirements, and aesthetic preferences specific to the industry or sector where the products will be utilized.
C. Cost Considerations
Economic factors play a significant role in the decision-making process. Different surface finishing techniques come with varying costs, including material expenses, processing expenditures, and potential maintenance costs. Balancing budget constraints with desired outcomes is integral to the decision-making process.
D. Regulatory Compliance
Adherence to regulatory standards and environmental considerations is increasingly becoming a decisive factor. Surface finishing methods must align with industry regulations and environmental guidelines, necessitating a careful evaluation of the environmental impact and compliance requirements.
Choose Our Die Casting Services
Choose our die casting services for unparalleled precision, reliability, and innovation. With a commitment to excellence, our state-of-the-art facilities and skilled team ensure the highest quality in every aspect of the die-casting process. Benefit from cutting-edge technology, personalized solutions tailored to your unique requirements, and a track record of delivering superior results. Whether you need intricate components for aerospace, automotive, or consumer electronics, our die-casting services guarantee optimal performance and durability. Elevate your manufacturing capabilities with a partner dedicated to exceeding expectations and delivering precision-engineered solutions.
Conclusion
In concluding our exploration of surface finishing for aluminum die castings, it becomes evident that the choice of finish is pivotal. From anodizing to powder coating, each technique brings its unique benefits, influencing aesthetics and functionality. By comprehensively considering material characteristics, end-use applications, cost implications, and regulatory compliance, manufacturers can make informed decisions. In the dynamic landscape of die casting, surface finishing stands as a transformative step, ensuring not only visual appeal but also durability and performance. As industries evolve, so do surface finishing technologies, promising a future where excellence in aluminum die castings is synonymous with meticulous surface treatment.
FAQs
1. What are the most common surface finishing for aluminum die castings?
The most prevalent surface coating options for aluminum die castings include anodizing, powder coating, chromate conversion coating, and electrophoretic painting. Each method offers unique benefits, addressing aesthetic, protective, and functional requirements.
2. What is PVDF coating on aluminum?
PVDF coating, or polyvinylidene fluoride coating, is a high-performance finish applied to aluminum surfaces. Renowned for its exceptional durability, weather resistance, and chemical stability, PVDF coating enhances the protective qualities of aluminum, making it ideal for outdoor applications and harsh environments.
3. How does anodizing contribute to the durability of aluminum die castings?
Anodizing forms a durable oxide layer on the surface of aluminum die castings, significantly enhancing their corrosion resistance and hardness. This process not only protects against environmental factors but also contributes to the overall longevity and durability of the die-cast components.