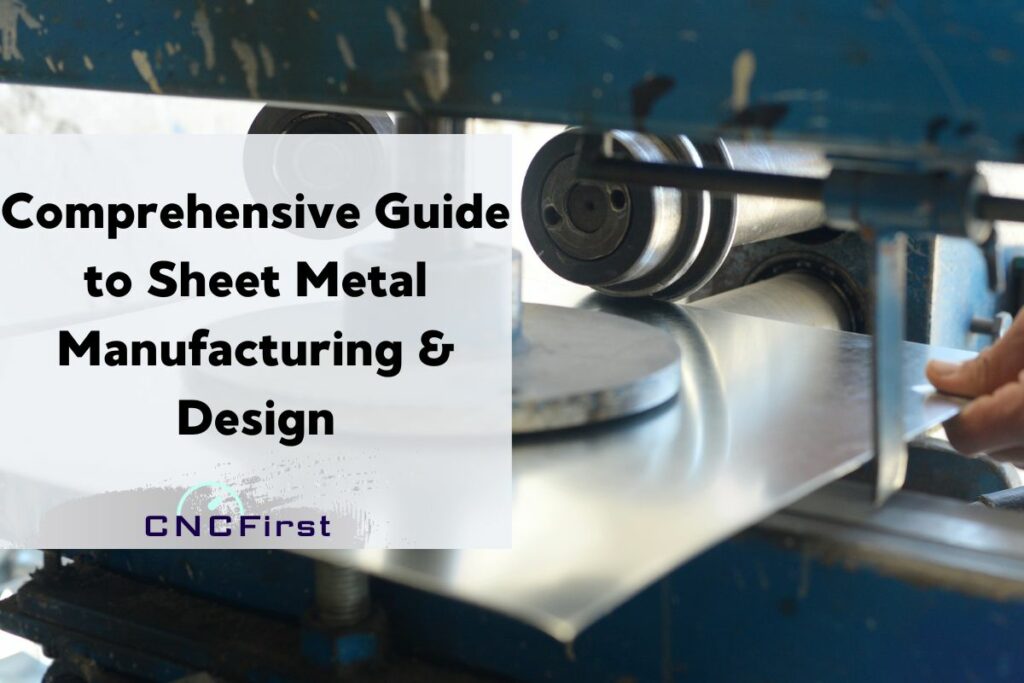
What do cars, airplanes, and appliances have in common? They’re all made of sheet metal! Sheet metal is a thin piece of metal that is used to make a variety of products. Sheet metal manufacturing is a process that has been used for centuries to create objects from thin pieces of metal. The design of the Sheet metal and the manufacturing process are integral parts of getting a high-quality product.
This blog post will discuss the sheet metal fabrication process and tips for getting the best results. Stay tuned!
How is Sheet Metal Being Used
Sheet metal is a broad-spectrum material that can be used for various applications. In its simplest form, sheet metal is a thin piece of metal that has been shaped into a flat sheet. It can be cut, stamped, sheared, shaped, bent, welded, rolled, riveted, drilled, tapped, and CNC machined. Shearing, or die cutting, refers to a process that cuts sheet metal without burning or melting it.
Sheet metal is most commonly made from stainless steel, but it can also be made from aluminum, brass, copper, or other metals. When working with sheet metal, it is necessary to wear gloves and eye protection to avoid cuts and scratches.
Steps:
- Measure and mark the desired dimensions on the sheet.
- Use a saw or shears to cut the sheet along the marked lines.
- Use a hammer or mallet to bend sheet metal into shape.
- Use a drill or punch to create holes for rivets or screws.
Following these simple steps, you can efficiently work with sheet metal to create custom parts and pieces for your next project.
Common Sheet Metal Forming Process
The metal sheet forming process involves three-dimensional manufacturing objects by metal bending, laser cutting, and assembling metal sheets. This process is widely used in the automobile industry, aircraft industry, and consumer electronics industry. The most common sheet metal forming processes are PRESS BRAKE BENDING, ROLL FORMING, STAMPING, and DRAWING.
Press Brake Bending
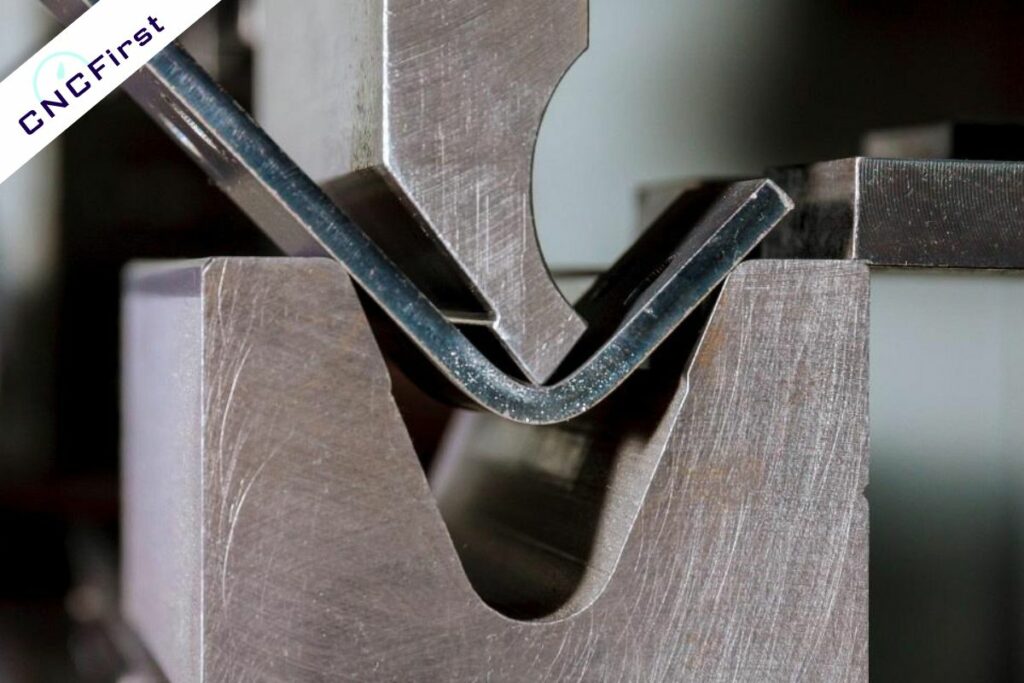
Press brake bending is a process of bending a metal sheet by applying pressure.
The pressure is exerted by the press brake machine, which has two dies – an upper die and a lower die.
Steps:
- The upper die is fixed while the lower die moves up and down.
- The metal sheet is placed between the two dies
- The lower die moves down
- Bends the sheet as per the desired shape.
Application:
Manufacturers can quickly and easily create parts such as fenders, doors, and engine mounts using a press brake.
Press brake bending is also frequently used in the construction industry to create metal roofs, siding, and beams.
Roll Forming
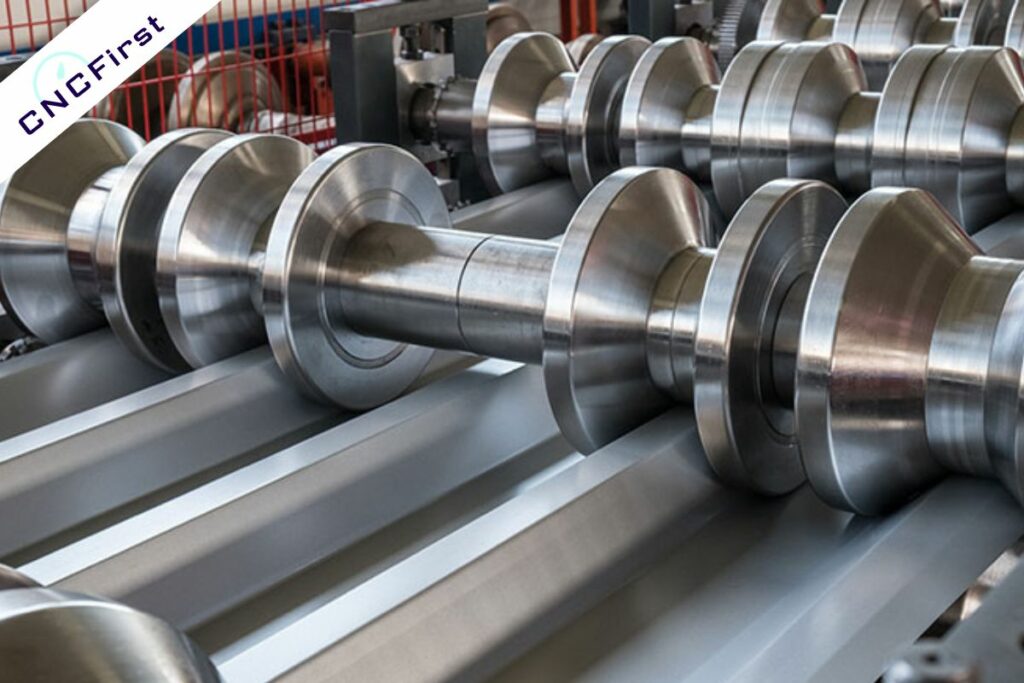
Roll forming is a process of shaping a metal sheet by passing it through a set of rollers.
Steps:
- The sheet passes through the rollers.
- Take the shape of each roller successively.
- Take the final desired shape.
Application:
Roll forming is used to create long objects, such as beams, pipes, etc., from a metal sheet.
Stamping
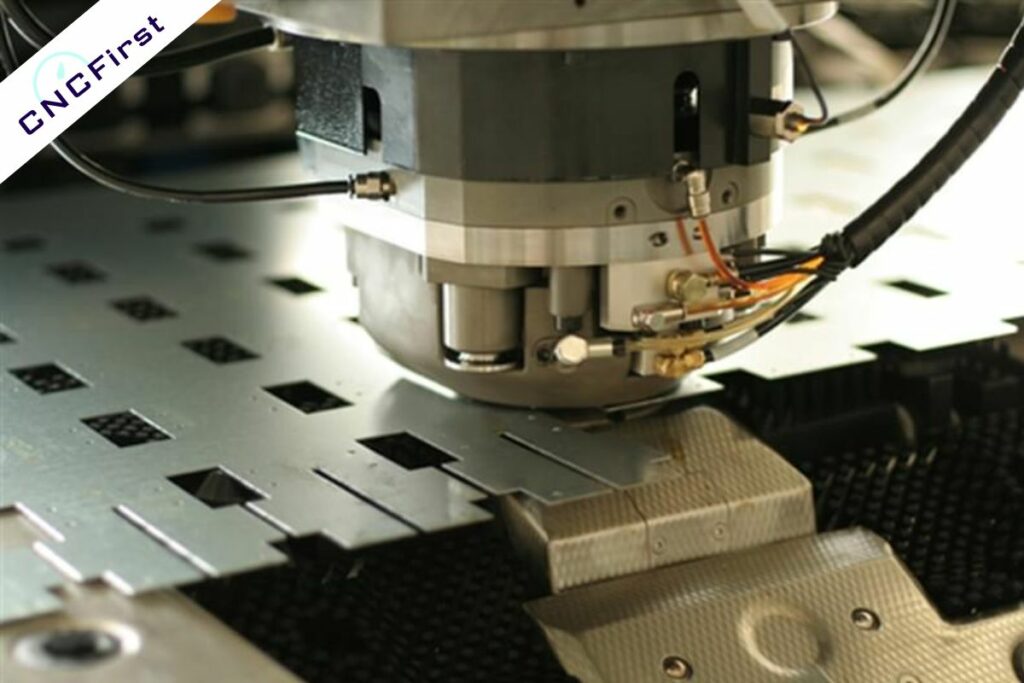
Stamping is a process of creating shapes or designs on a metal sheet by using stamps.
The stamps are made of hardened steel and have a negative image of the required design or shape.
Steps:
- Place the stamp on the metal sheet
- Hit with a hammer.
- Create an impression on the sheet.
Application:
Stamping is commonly used in the manufacturing industry to decorate and personalize parts and products. It can also be used for other applications, such as creating artwork, decorating tools and appliances, and even jewelry making.
Drawing
Drawing is a process of stretching a metal sheet to create hollow objects such as tubes, pipes, etc. This process is also known as the deep drawing or cup drawing process.
Steps:
- A die with a negative image of the desired hollow object is placed on the metal blank.
- The blank stretched over the die using hydraulic pressure
- Take the shape of a negative image in the die.
Application:
In the aerospace industry, metal stretching is often used to create lightweight parts with a high degree of strength and stiffness.
In the medical field, metal stretching is sometimes used to create artificial implants and prosthetics..
Design Considerations For Sheet Metal Fabrication
When it comes to sheet metal fabrication, a few key design tips and considerations need to be kept in mind to ensure a successful outcome.
- It’s important to choose the right type of metal for the project.
Different metals have different properties that make them more or less suited for specific applications.
For instance, aluminum is a good choice for projects that require lightweight and corrosion resistance, while steel is better for projects where strength and durability are more important.
- It’s essential to consider the type of metal you’ll be using. Different metals have different properties that will affect the fabrication process.
For example, aluminum is famous for sheet metal fabrication because it’s lightweight and corrosion-resistant. However, it’s also more challenging to work with than other metals.
- It’s essential to consider the thickness of the metal.
Thicker metal sheets are more challenging to cut and form, so choosing a thickness that will work well with your desired end product is important.
- You’ll need to take the finish of the metal into account.
A high-quality finish will improve the look and feel of the final product, but it can also add to the cost of fabrication.
By taking all of these factors into account, you can be sure to select the best possible approach for your particular project.
Surface Finishes For Sheet Metal Manufacturing
When it comes to sheet metal fabrication, a variety of surface finishes can be applied to the material.
Some common finishes include powder coating, anodizing, and plating. Each of these finishes provides a different level of protection against corrosion and wear, and they can also be used to achieve a desired aesthetic effect.
Powder coating
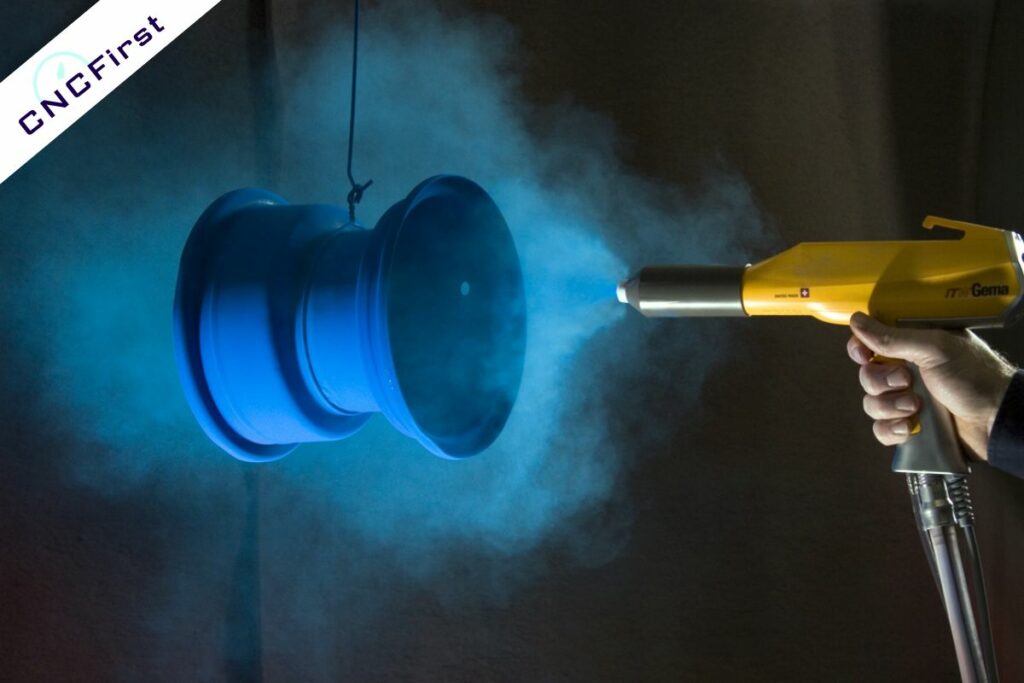
The process of powder coating as a dry powder and then curing at high temperatures creates a rigid, smooth surface. Powder coating is famous for sheet metal fabrication, providing a durable and attractive finish.
Anodizing
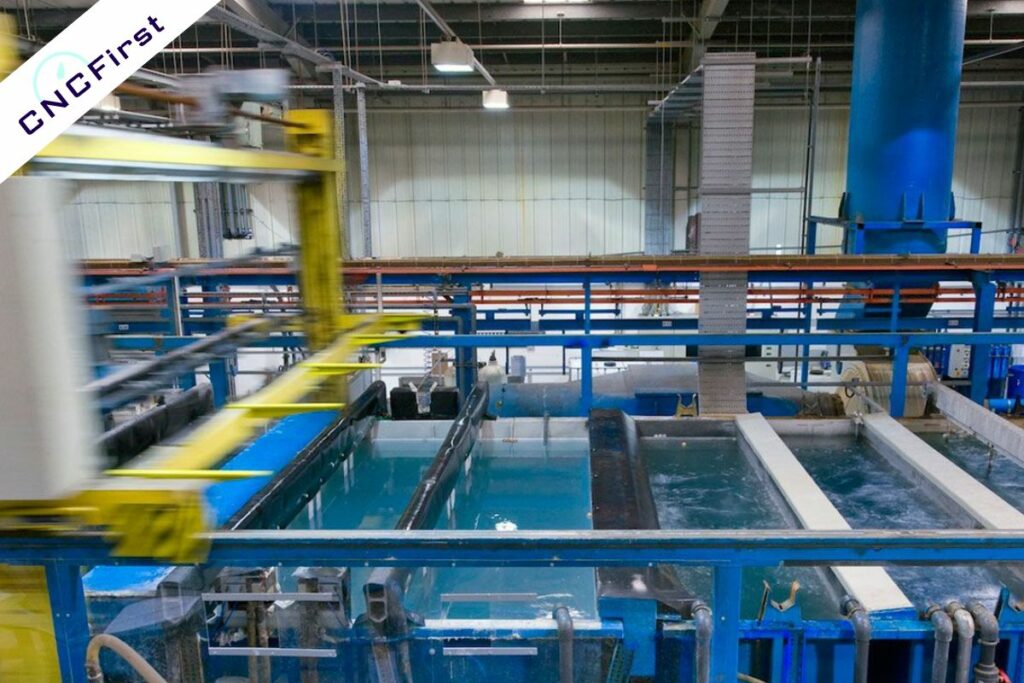
Anodizing is a process in which the material is exposed to an electric current, which causes a thin oxide layer to form on the surface of the metal. This oxide layer helps to prevent further corrosion of the material. Anodizing can help protect the material from corrosion and wear.
Plating
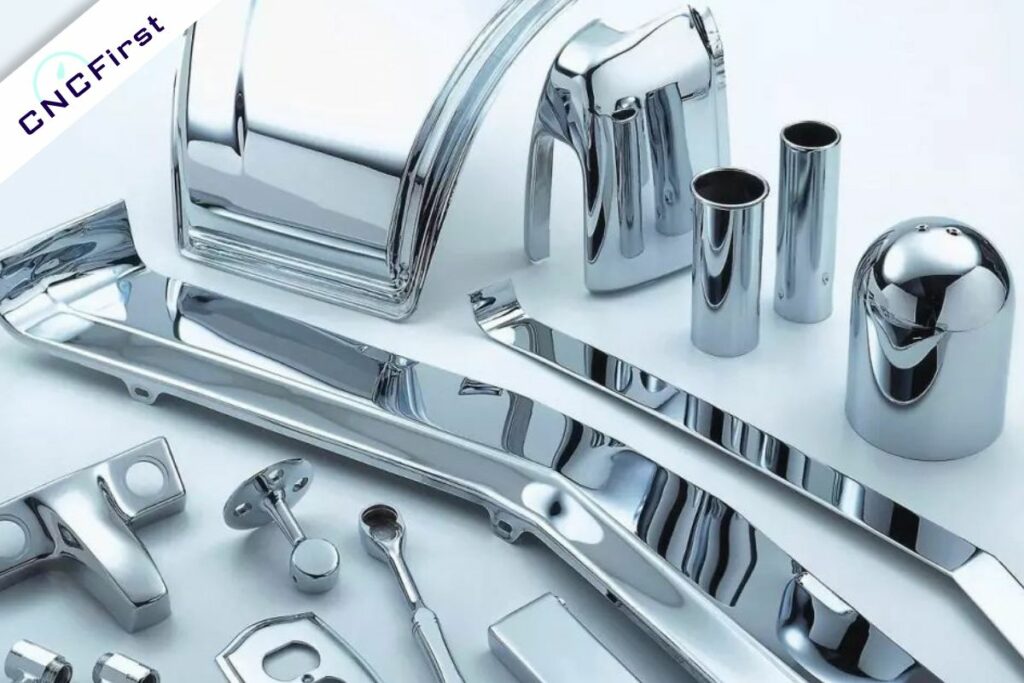
Plating is a process in which a thin layer of metal is deposited onto the surface of the sheet metal. This layer can be either decorative or protective.
Plating is often used to give sheet metal a desired aesthetic effect, as it can be used to add a lustrous finish to the material.
Applications Of Sheet Metal Fabricated Parts
Automotive
Sheet metal fabricated parts are used extensively in the automotive industry for functional and decorative purposes.
Common examples of automotive applications for sheet metal fabricated parts include fenders, hoods, doors, and trunk lids. Sheet metal fabricated parts can also be used to create interior trim pieces, such as dashboards and door panels.
In addition, many automotive manufacturers use sheet metal to create custom grilles and other exterior styling elements.
Healthcare
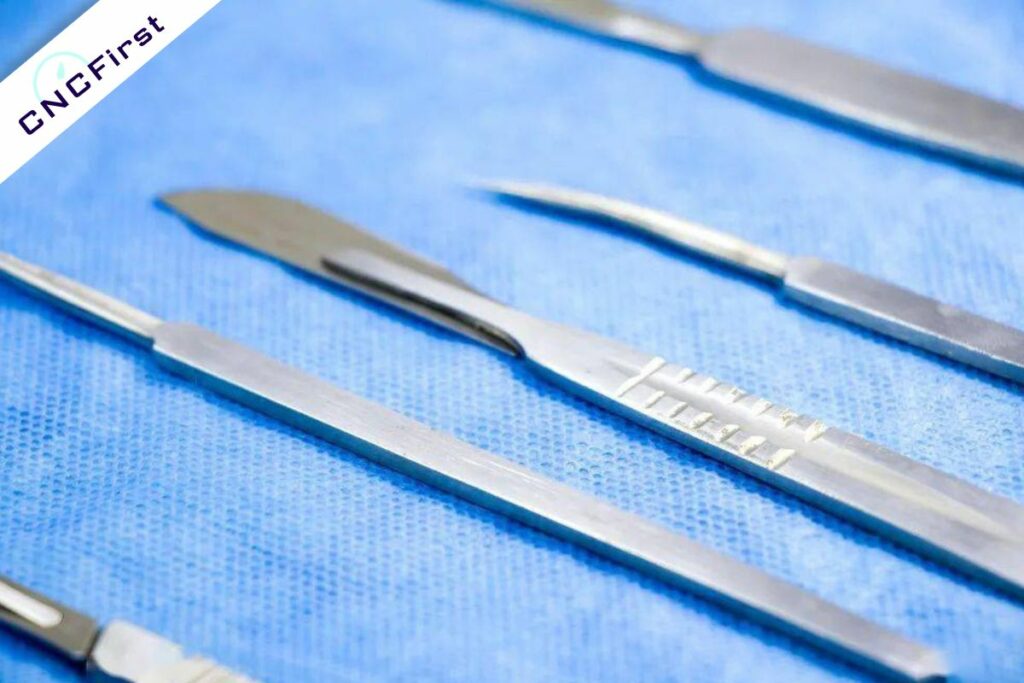
There are many different healthcare applications for sheet metal fabricated parts. Sheet metal fabricated parts can be used in medical devices such as X-ray machines and MRI machines.
Fabricated parts can also be used in hospital equipment, such as IV stands and examination tables.
In addition, fabricated parts can be used to create prototypes for new medical devices and products.
Aerospace
In order to meet the stringent requirements of the aerospace industry, manufacturers of sheet metal fabricated parts are constantly innovating and developing new methods and technologies.
One area that has seen significant progress in recent years is the use of computer-aided design (CAD) and computer-aided manufacturing (CAM) to create high-precision components.
The technology not only helps to reduce the time and cost of production, but it also allows for greater control over the final product.
As a result, CAD/CAM-generated parts are increasingly used in various aerospace applications, from engine components to fuselage panels.
Consumer Electronics Industry
Household appliances and consumer electronics are two main markets for sheet metal fabricated parts.
One of the most common uses for sheet metal parts in consumer electronics is the manufacture of electronic device enclosures. Sheet metal parts can be used to create both the exterior and interior components of an enclosure and the use of different metals can provide a variety of looks and finishes.
Sheet metal fabricated parts can also be used to create a variety of other components, such as brackets, standoffs, heat sinks, and ventilation grilles.
As the demand for new and innovative consumer electronics increases, so does the need for high-quality sheet metal fabrication services.
Conclusion
Sheet metal manufacturing is a process that involves the cutting and shaping of metals. The design of sheet metal components is important to consider during the manufacturing process. There are miscellaneous factors that need to be considered when designing sheet metal components, such as strength, weight, aesthetics, and function.
No matter what design or manufacturing process you choose for your sheet metal product, we can all help you.
We have years of experience and a commitment to quality that is second to none in the industry.
Contact us today to learn more about how we can serve you.