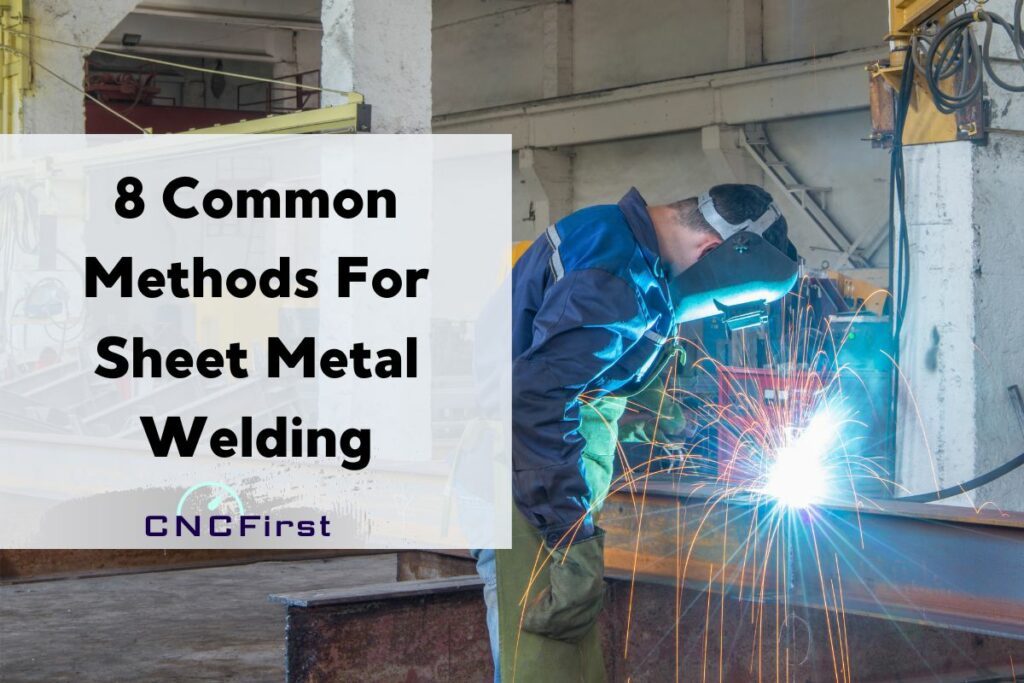
Sheet metal welding is a critical process in many industries. It can be used to create and fix objects made from metal sheets. There are a few common methods of welding sheet metal, each with its strengths and weaknesses.
In this blog post, we’ll take a look at the most common methods of welding sheet metal and some techniques for getting the best results. Let’s get started!
What Is Sheet Metal Welding
Sheet metal welding is a process of sheet metal fabrication that’s used to join together two pieces of metal.
The process involves heating up the pieces of metal until they’re soft enough to be joined, then using pressure and heat to weld them together.
There are 8 methods of sheet metal welding commonly used today: spot welding, tungsten inert gas (TIG) welding, metal inert gas (MIG) welding, skip welding, flux-cored arc welding (FCAW), resistance welding, ultrasonic welding, and tack welding.
No matter which type of sheet metal welding you choose, it’s essential to follow safety precautions and practice scrap metal before trying it on a project. With a bit of practice, all people can master the art of sheet metal welding.
Method1: Spot Welding
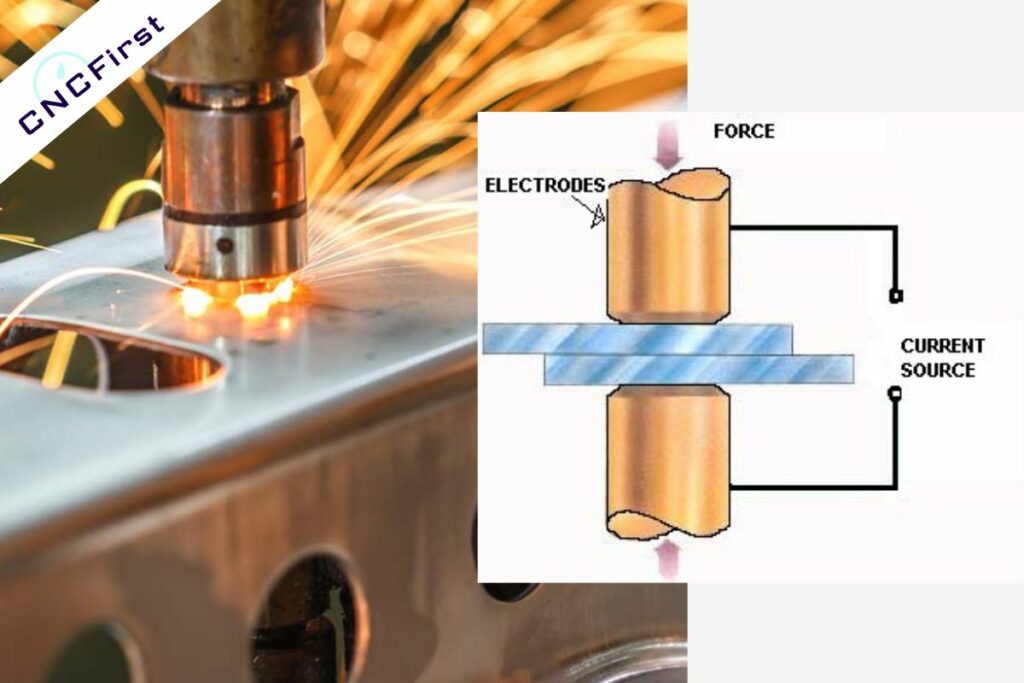
Spot welding is a welding type that is commonly used to join metals together.
The process involves using electrical current to heat up two metal surfaces until they are melted together.
This can be done by passing an electric current through the metal surfaces or using an electrode to create a localized hot spot.
The key to spot welding is applying enough heat to the metal surfaces to melt them together without causing any damage to the surrounding area.
In addition, spot welding is often used in conjunction with other welding processes, such as MIG welding, in order to create more robust and reliable welds.
Application:
Spot welding is often used in the manufacturing of automobiles and other products.
Method2: TIG Welding
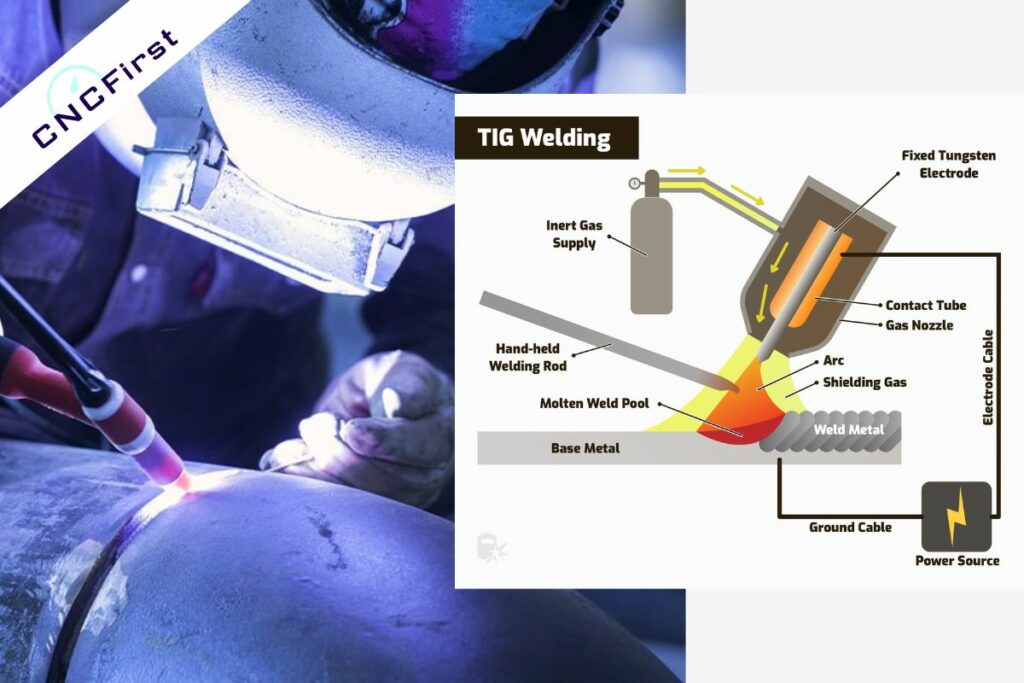
TIG welding is a welding type that uses an arc between a non-consumable tungsten electrode and the metal being welded. The electrode and the metal are both melted by the heat of the arc and then cooled to create a strong bond.
TIG welding can be used on various metals, including aluminum, stainless steel, and magnesium.
TIG welding is also relatively easy to learn, making it a popular choice for hobbyists and DIYers.
Application:
TIG welding is typically used when high-quality welds are required, such as in aerospace or automotive applications.
Method3: MIG Welding
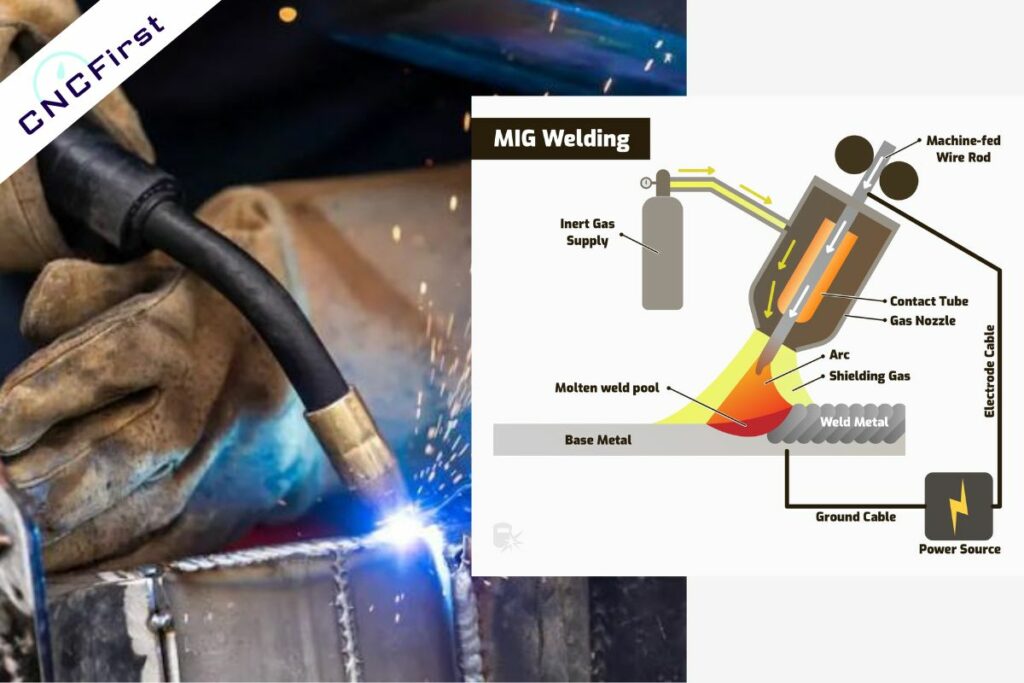
MIG welding is a welding technique type that uses an electric arc to join metals. The arc is created by an electrode that is fed through a welding gun and is attached to the workpiece.
The electric pole is made of a consumable wire that melts as it hits the workpiece, creating a weld pool. MIG and TIG welding methods are best suited for flat surfaces.
Application:
MIG welding is commonly used to join steel, aluminum, and stainless steel. It is also possible to weld other metals, such as copper and nickel.
It is often used in automotive and construction applications.
Method4: Skip Welding
Skip welding is a technique used in welding that involves leaving gaps in the joint instead of welding the entire length of the joint. This method is used to minimize the amount of heat input and to reduce the risk of warping and distortion in the joint. The gaps, or skips, are strategically placed to enable the welder to achieve a strong and stable joint, without the need for continuous welding.
Application:
This technique is commonly used in structural welding, where heavy-duty welding is required. Skip welding is also used in cases where aesthetics are important, as it allows the welder to achieve a tidy and uniform appearance of the final weld.
However, it must be noted that skip welding requires a high level of skill and expertise, as the gaps must be placed carefully and the welds must be strong enough to support the joint.
Method5: FCAW Welding
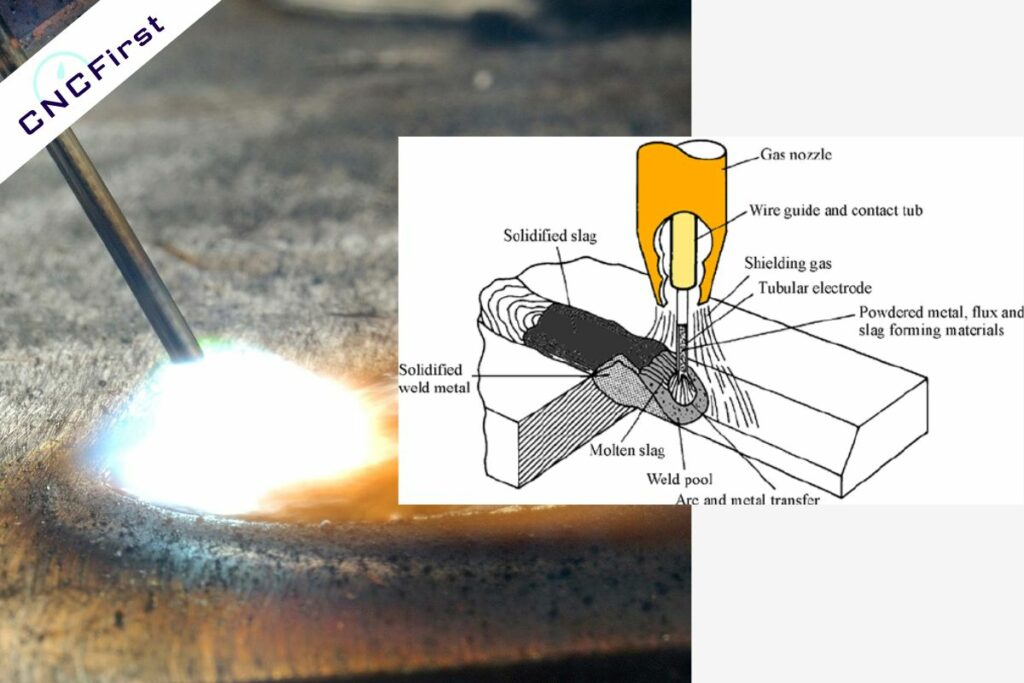
FCAW welding is a welding type that uses a continuous wire feed. FCAW welding can be performed with either AC or DC power sources and use either gas-shielded or self-shielded wire.
The process is like MIG welding but does not require the use of shielding gas. This makes FCAW welding more versatile, as it can be used in a fantastic range of applications.
Application:
FCAW Welding is often used for outdoor applications, as it is less likely to be affected by windy conditions.
Method6: Resistance Welding
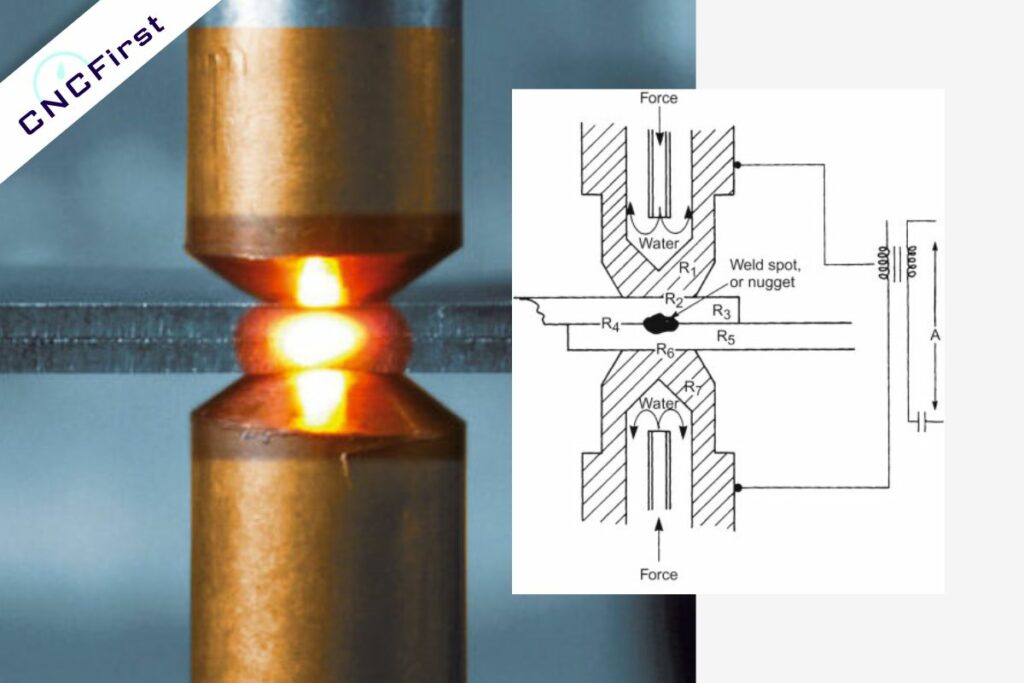
Resistance welding is a welding type that uses electrical resistance to heat the metals being joined. The area where the metals contact each other is heated by the resistance of the metals to the flow of electricity.
In order for resistance welding to occur, there must be contact between the two pieces of metal, sufficient pressure to create a good electrical connection, and an electrically conductive path between the two pieces of metal.
The most common forms of resistance welding are spot welding and seam welding.
Application:
Resistance welding is a versatile and efficient way to join metal, and it can be used on various materials, including steel, aluminum, and copper.
Method7: Ultrasonic Welding
Ultrasonic welding is a diffusely used joining method in which high-frequency vibration is used to create frictional heat at the boundary surface of two parts to be joined.
Ultrasonic welding is a fast, efficient, and relatively clean way to combine two pieces of material. Additionally, it can be performed without the use of filler materials or external heat sources.
Application:
Ultrasonic welding can be used on various materials, including metals, plastics, and composites.
Method8: Tack Welding
Tack welding is a temporary type of welding used to hold two or more pieces of metal in place before the final weld is made. It involves using small welds to hold the pieces together without adding too much heat or melting the metal completely.
Application:
Tack welding is often used in sheet metal work, pipe fitting, and construction to ensure that the pieces are aligned and properly positioned before proceeding with the final weld. It allows the welder to make any necessary adjustments before committing to the final weld, which can save time and reduce the risk of mistakes.
Once the tack welds are in place, the welder can then proceed with the final weld, creating a sturdy and secure joint between the pieces of metal.
Related Article:
Sheet Metal Design Guide For Product Manufacturing
Sheet Metal Laser Cutting: What You Need To Know
Advantages And Disadvantages Of Sheet Metal Welding
Each method has pros and cons, making it more or less suitable for different applications. The following table summary can help you understand better.
Method | advantages | disadvantages |
Spot Welding | fast and relatively inexpensive | not as strong as other types of welding only be used on certain metals |
TIG Welding | more powerful | more expensive and time-consuming |
MIG Welding | similar to TIG welding in terms of strength and versatility | easier to learn and faster to execute |
Plasma Cutting | a very powerful form of cutting | produces a lot of heat and can be dangerous if not done properly |
FCAW Welding | less expensive than TIG or MIG welding | more difficult to control |
Resistance Welding | fast and efficient | difficult to achieve a consistent result |
Ultrasonic Welding | very fast and efficient | expensive |
Tips For Sheet Metal Welding
When it comes to welding thin sheet metal, there are a few things you need to keep in mind in order to get the best results.
- It would be better if you use the proper welding process. For thinner metals, MIG or TIG welding is usually the best option. If you’re working with thicker metal, you’ll likely need to use stick welding.
- It would be better if you used the correct welding rod. The type of rod you use will depend on the metal you’re welding and the thickness of the metal.
- It would be better if you be aware of expansion and contraction. When welding sheet metal, it’s essential to allow for expansion and contraction by leaving enough space between welds.
- It would be better if you had a good grasp of heat control. Too much heat can damage the metal or cause warping.
By following these tips, you can guarantee a successful weld every time.
Conclusion
Now that you know the most common types of welding methods used to weld sheet metal, as well as some tips and knacks for getting started, you’re ready to start your welding project.
No matter which way you choose, it’s critical that you have the right tools and materials for the job.
We provide a wide range of services, including custom fabrications, cut-to-size pieces, just-in-time delivery, and more. Contact us today if you require help finding the perfect solution for your next welding project. Our teamwork would be happy to assist you.