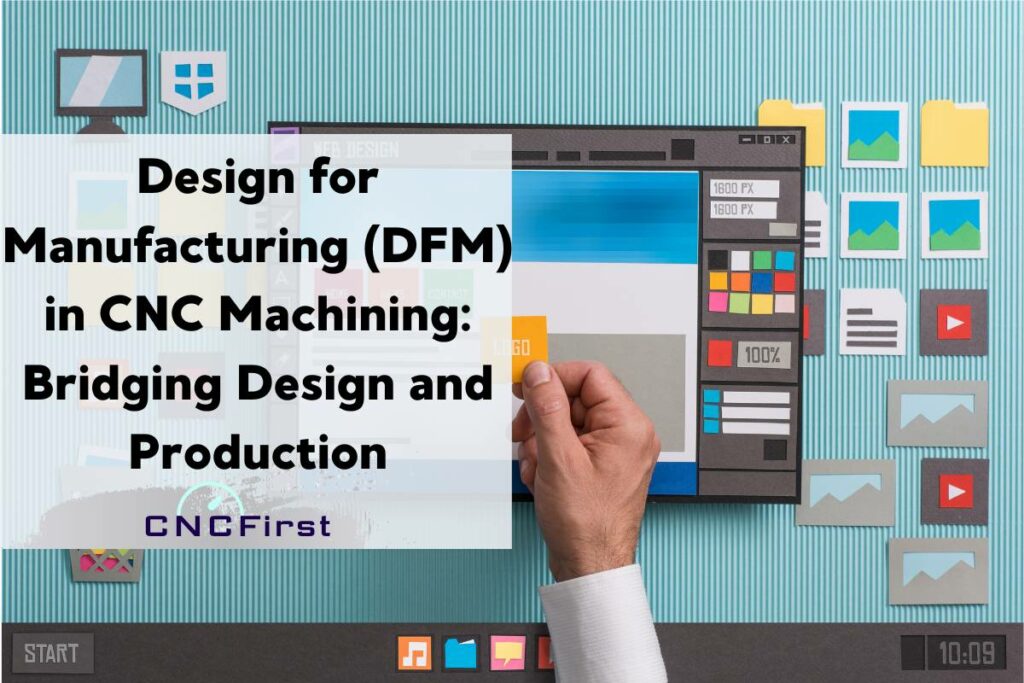
In today’s competitive manufacturing landscape, “Design for Manufacturing” has become a buzzword synonymous with efficiency and cost-effectiveness. By integrating DFM principles, CNC machining can harmonize innovative designs and practical manufacturability.
This article delves deep into understanding DFM’s role in CNC, shedding light on its principles, benefits, and best practices. Furthermore, drawing from real-world case studies, it emphasizes the significance of collaboration between designers and CNC machinists.
As we journey through this topic, we’ll also tap into expert resources on manufacturing principles, a comprehensive guide to CNC machining, and authoritative information on manufacturing standards.
The Essence of Design for Manufacturing in CNC Machining
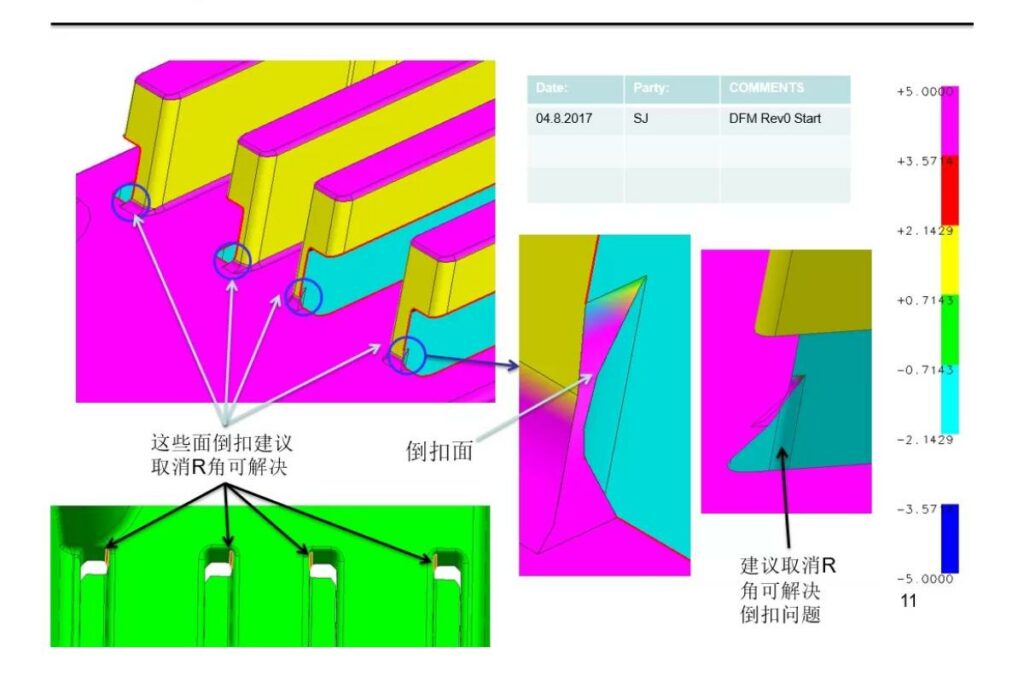
When we speak of “Design for Manufacturing,” we refer to the systematic approach to simplify product structures, ensuring easier, more cost-effective production. Especially in CNC machining, this methodology becomes crucial. Not only does it determine the manufacturability of a design, but also its longevity and functional efficiency.
The focus isn’t merely on creating a design that looks good on paper or in a digital model. Instead, it’s about understanding the nuances of the CNC machine’s capabilities, the intricacies of materials, and the hands-on experience of the machinists. The synergy of these factors ensures that a design transitions smoothly from a concept to a tangible product.
Practical Benefits of Implementing DFM in CNC
The advantages of embedding DFM principles into CNC processes are manifold. Firstly, it reduces production costs. Preemptively identifying and resolving potential manufacturing issues in the design phase minimizes waste of resources and time. It further results in products with fewer defects, leading to a reduced need for post-production corrections.
Moreover, DFM practices enhance the overall efficiency of the CNC machining process. By eliminating unnecessary complexities in design, production cycles become more streamlined and faster. This time efficiency is invaluable in industries with tight production schedules. Customers can also take steps to optimize their CNC machined parts, such as designing by standard Design for Manufacturing (DFM) best practices.
Steps to Incorporate DFM in CNC Designs
Design for Manufacturability (DFM) is more than just a buzzword; it’s a systematic approach that bridges innovative concepts with practical manufacturability in CNC machining. Here’s a step-by-step guide on how to seamlessly integrate DFM principles into CNC designs:
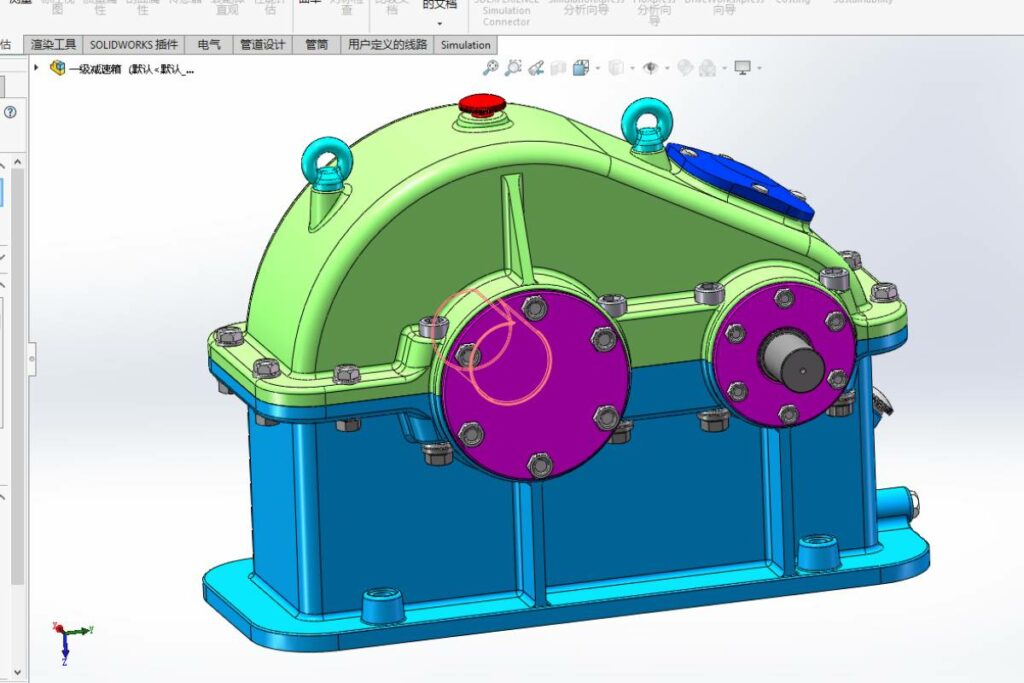
Analyzing the Initial Design:
The journey begins with a comprehensive evaluation of the initial design. This entails studying the blueprint for its form, function, and feasibility. It’s paramount to ask: while the design might appear ideal, is it optimized for manufacturing?
Identifying Potential Manufacturing Challenges:
Once the design is thoroughly analyzed, it’s time to spot potential manufacturing bottlenecks. These could range from intricate geometries that might be challenging to machines to selecting materials that might not behave as expected during the CNC process. By proactively pinpointing these hurdles, one can preempt costly production mishaps.
Iterative Design Modifications:
DFM is an iterative process. Based on the challenges identified, the design undergoes multiple refinements. This might mean simplifying certain aspects, modifying dimensions, or even rethinking some design components entirely. Each iteration brings the design closer to CNC-ready, balancing innovation with manufacturability.
Collaborating with CNC Machinists:
Lastly, and most importantly, is collaborating with the machinists at the heart of CNC operations. By bridging the gap between designers and machinists, real-world insights flow into the design process. Leveraging their hands-on experience ensures the design is functional and optimized for a smooth manufacturing journey.
Incorporating DFM into CNC designs isn’t just about efficiency; it’s about creating innovative and practical products. By following these steps, manufacturers can ensure a harmonious transition from design to product.
Common Mistakes to Avoid in DFM for CNC Machining
In CNC machining, the pursuit of perfect designs often leads to common pitfalls. While Design for Manufacturing (DFM) offers a structured pathway to marry creativity with manufacturability, certain oversights can jeopardize the process. Here are some prevalent mistakes and how to sidestep them:
Overcomplicating Designs:
The allure of intricate designs can be tempting. However, complexity only sometimes translates to functionality or manufacturability. Overly complex geometries can strain CNC machines, leading to longer machining times and increased wear. Simplifying designs without compromising on functionality ensures a smoother and more cost-effective production process.
Neglecting Material Constraints:
Every material has unique properties — from machinability to thermal tolerance. Designing without considering these constraints can lead to undesired outcomes, such as material warping or premature wear. It’s essential to choose materials that align with the design’s purpose and the capabilities of the CNC machine.
Overlooking Tolerance Limits:
Precision is the hallmark of CNC machining. However, disregarding the machine’s tight tolerance limits or setting unrealistic tolerances can lead to production hiccups. Setting realistic tolerances that align with the machine’s capabilities is crucial, ensuring consistent product quality without overburdening the equipment.
Steering clear of these pitfalls ensures that DFM for CNC machining remains a productive and efficient endeavor, creating innovative and ready designs for the production floor.
Frequently Asked Questions
1. What does DFM stand for in CNC machining?
DFM stands for “Design for Manufacturability.” CNC machining pertains to designing parts with the manufacturing process in mind, ensuring easy and cost-effective production.
2. How does DFM differ between CNC machining and other manufacturing methods?
DFM principles remain consistent across manufacturing methods, focusing on design optimization for production. However, the specific considerations can differ. CNC machining emphasizes machine capabilities, tool paths, and material removal, whereas other methods may focus on moldability or assembly ease.
3. Can DFM be applied retrospectively to existing designs?
Yes, DFM can be retroactively applied. This often involves analyzing current designs and making modifications to enhance manufacturability, potentially leading to cost and time savings.
4. How does DFM impact the final product quality?
By ensuring the design is optimized for manufacturing, DFM can lead to fewer defects, consistent production outcomes, and a higher overall product quality.
5. Why is collaboration between designers and machinists important in DFM?
Collaboration bridges the gap between design theory and practical manufacturing. Machinists provide valuable insights into real-world production challenges, ensuring innovative and manufacturable designs.
Design for Manufacturing (DFM) in CNC Machining – A Necessity for Modern Production
In the intricate dance of design and production, “Design for Manufacturing,” or DFM, is the choreographer, ensuring every move is precise, efficient, and harmonious. The importance of DFM can’t be overstated in the realm of CNC machining. It’s not just about crafting designs that are visually appealing or conceptually innovative; it’s about creating designs that can transition smoothly from the digital workspace to the manufacturing floor.
As we wrap up this exploration into DFM and CNC machining, it’s evident that for businesses aiming to lead the manufacturing frontier, understanding and implementing DFM isn’t just beneficial – it’s essential.